How to Measure and Increase Manufacturing Output
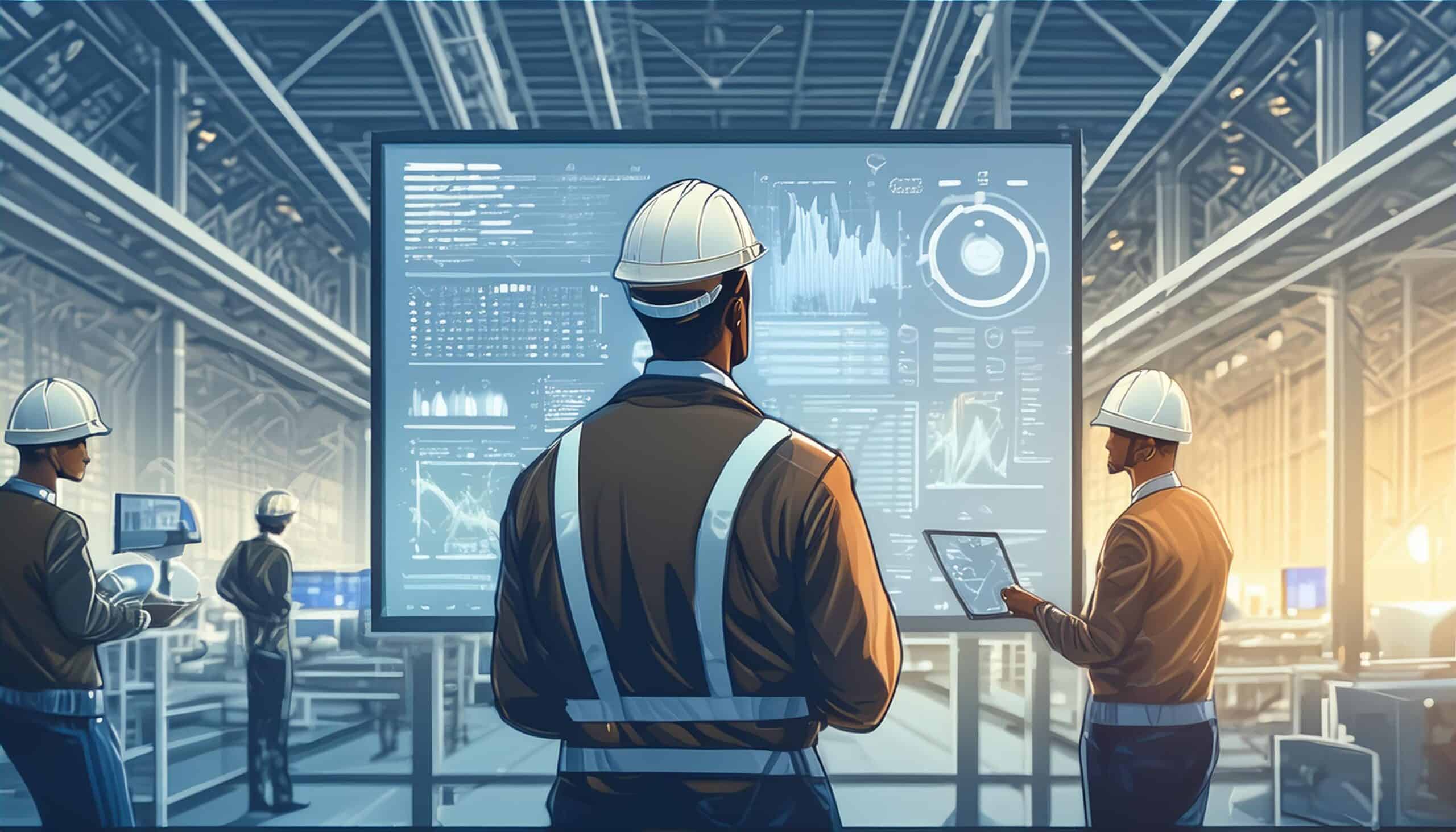
Increasing production output is a critical objective for any manufacturing business aiming to stay competitive.
One of the most effective ways to achieve this is by accurately measuring and increasing manufacturing output. Understanding the key metrics and implementing strategies to enhance efficiency can lead to significant improvements in both productivity and quality.
In this article, we’ve created a detailed project plan that outlines strategic initiatives for increasing production output over the next 12 months in your factory.
Boost Production Output
Maximise efficiency with our Digital Transformation Starter Kit. Access strategic guides and templates to enhance your factory’s output. Download now and start optimising.
In this article:
Goals & Project Team
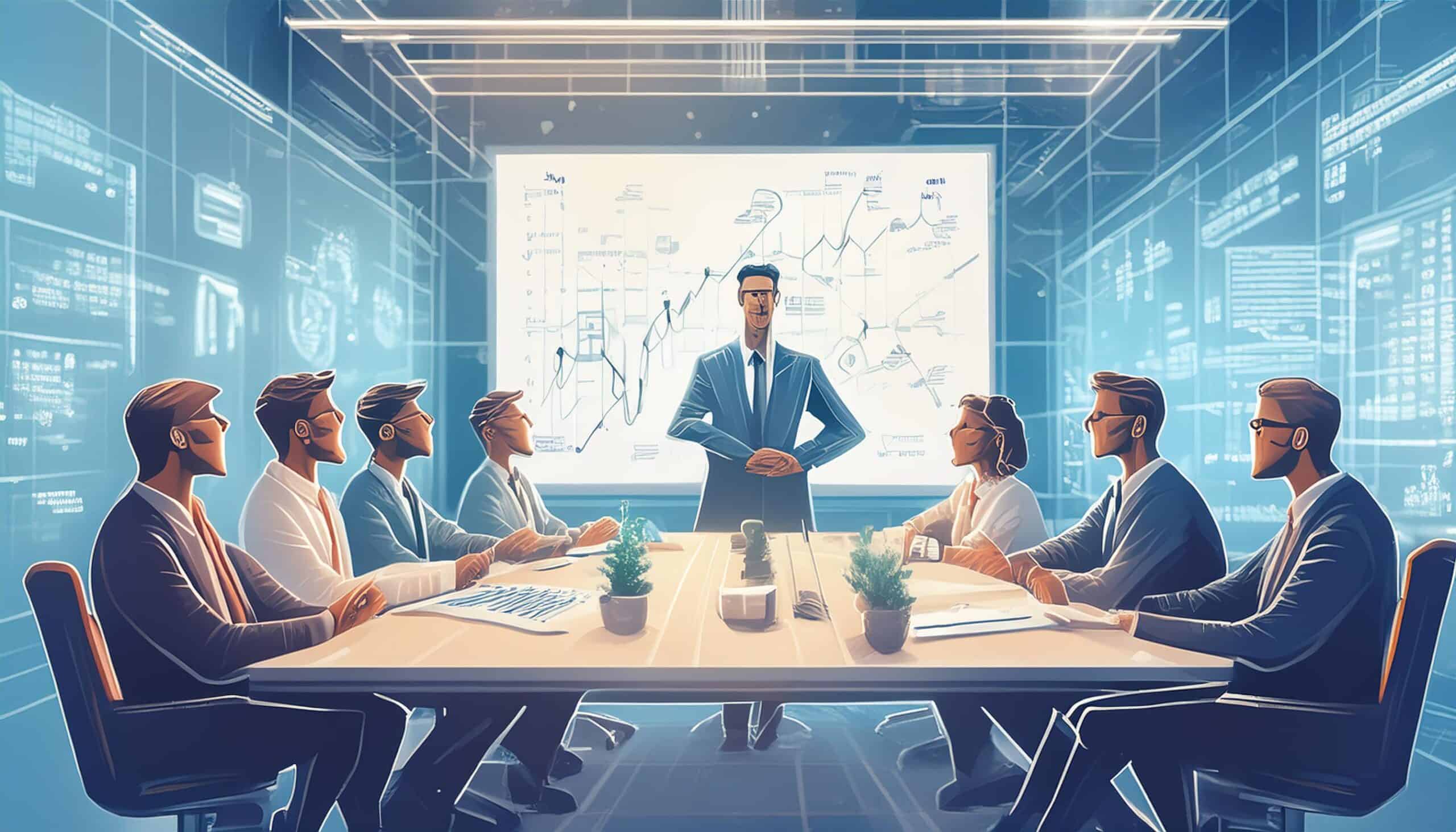
Start by establishing clear goals and form a project team.
Set specific, measurable, achievable, relevant, and time-bound (SMART) goals for the project.
Assemble a cross-functional team, including project managers, production managers, engineers, IT specialists, and key operators.
Enhance Operational Efficiency
Elevate your production with our Digital Transformation Starter Kit. Download now for expert resources to refine your manufacturing processes.
Planning
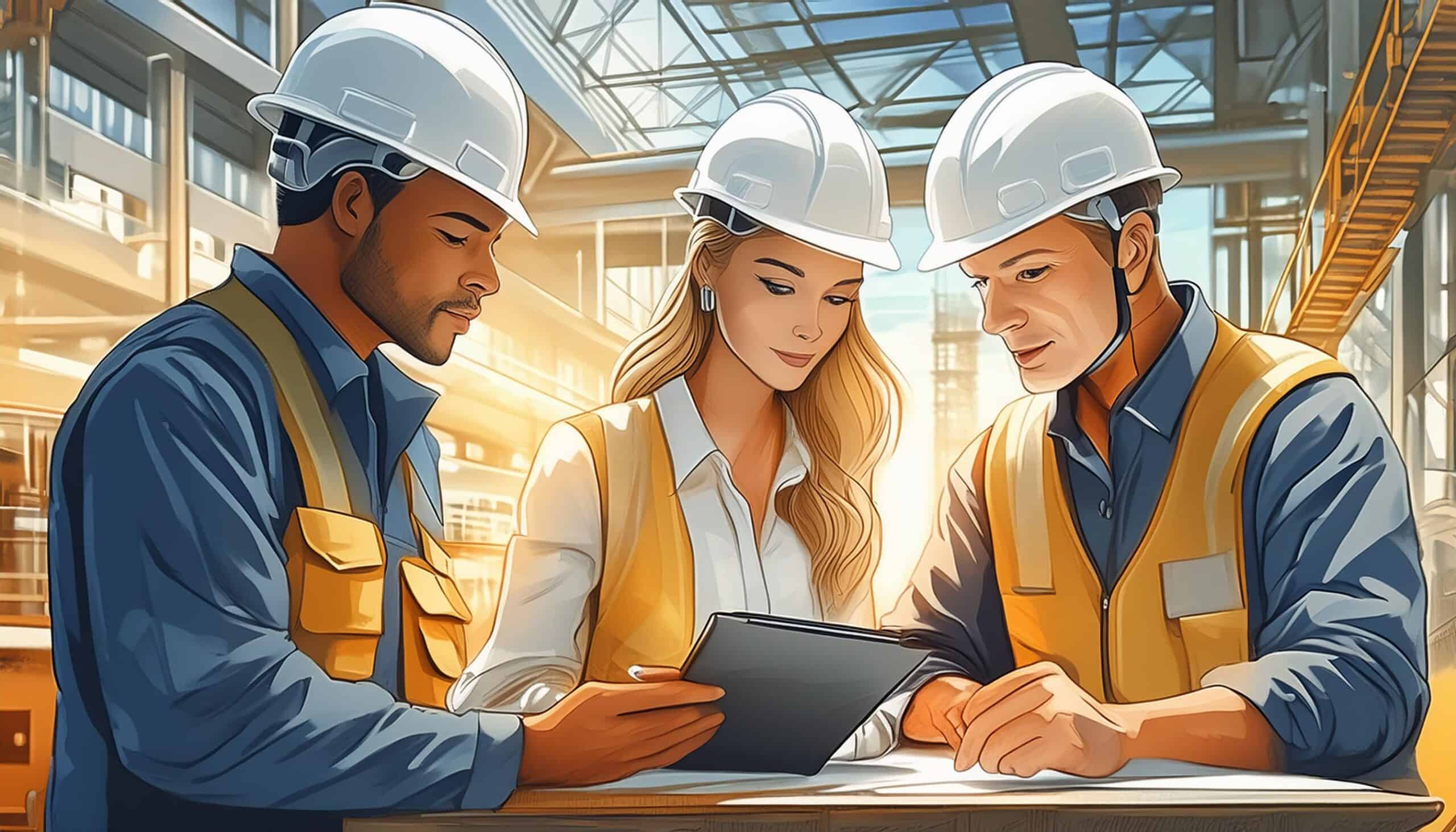
Creating a thorough project plan will help to map out the project from start to finish. The project plan should include:
Conduct a thorough analysis of current production processes, equipment efficiency, and workforce capabilities.
Establish key performance indicators (KPIs) such as Overall Equipment Effectiveness (OEE), cycle time, and throughput.
Identify and allocate necessary resources, including budget, personnel, and technology.
Perform a risk assessment and develop mitigation strategies.
Implementation
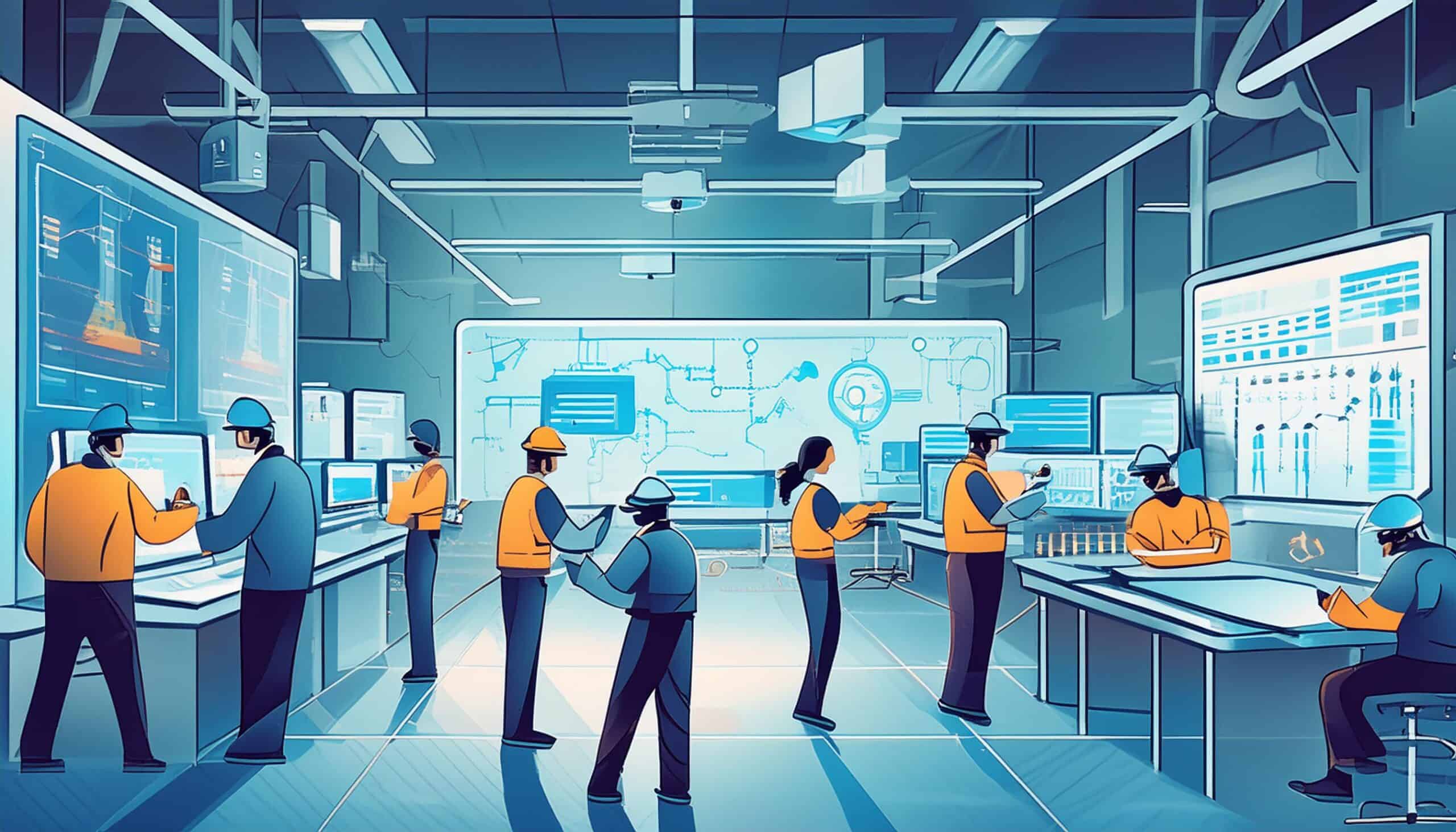
Now you are ready to start implementing the project to increase production output. These are my suggestions of the top activities to undertake to increase production output, you can pick one or multiple techniques to implement from each section.
Process Optimisation
Implement lean manufacturing principles such as 5S, Kaizen, and value stream mapping to eliminate waste and streamline processes.
Redesign workflows to reduce bottlenecks and improve process flow.
Update and standardize SOPs to ensure consistency and efficiency.
Utilise Tascus‘ Digital Work Instructions to standardise and update SOPs across the factory for improved efficiency.
Technology Enhancement
Install and integrate automated monitoring systems for real-time data collection.
Implement AI-powered predictive maintenance tools to reduce downtime.
Introduce IoT devices, robotics, and other advanced technologies to automate repetitive tasks.
Gain complete visibility of your manufacturing process with Tascus’ Real-Time Visibility feature to track the status of products as they move through the factory.
Workforce Efficiency
Develop and deliver comprehensive training programs focused on new technologies and lean manufacturing techniques.
Foster a culture of continuous improvement through regular feedback sessions and incentive programs.
Establish cross-functional teams to drive innovation and process improvements.
Enhance workforce efficiency with Tascus’ Digital Manufacturing Travelers to ensure full traceability and compliance with ease.
Supercharge Your Production Process
Advance production with our Digital Transformation Starter Kit. Download now for essential tools and resources to optimise your operations.
Monitoring & Wrap Up
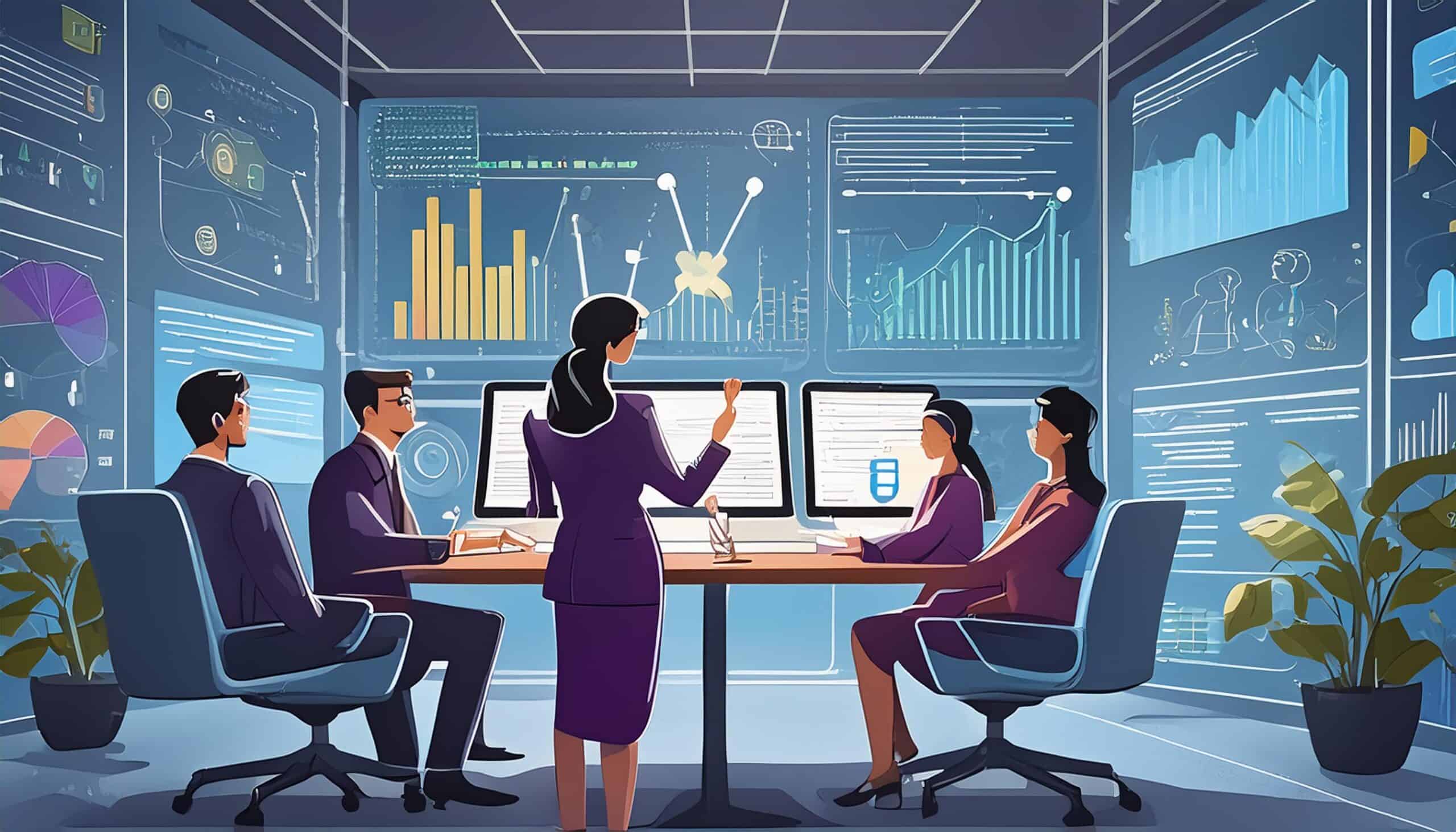
Once you’ve started the implementation phase of the project, it’s important to measure what matters and keep on top of progress.
Conduct monthly progress reviews against KPIs to track performance and identify areas needing adjustment.
Utilise data analytics to continuously monitor production metrics and adjust strategies as needed.
Encourage a culture of continuous improvement by implementing suggestions from employees and stakeholders.
Acknowledge and celebrate the efforts and successes of the project team and all involved employees.
Key Milestones
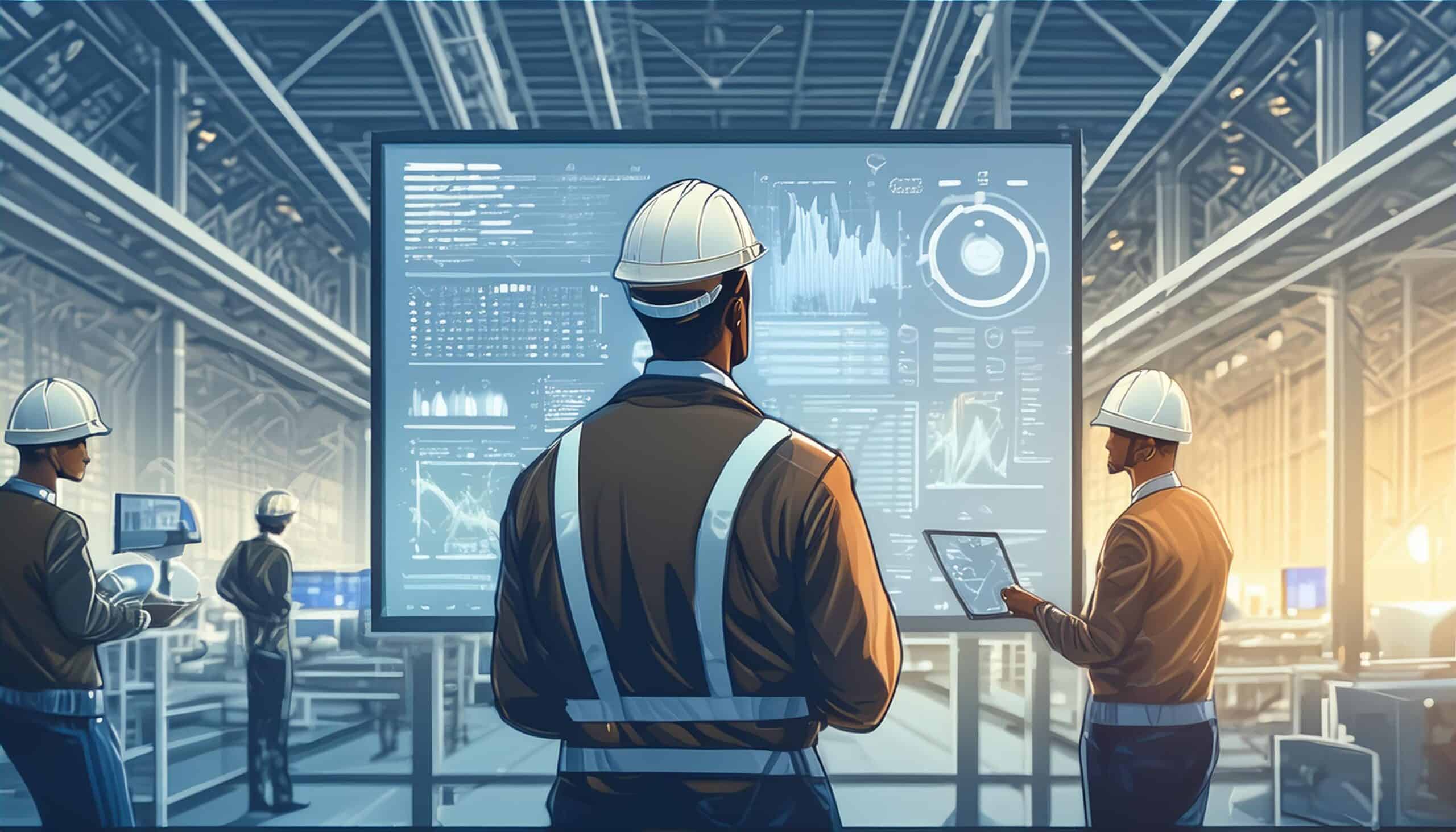
To help track progress in this manufacturing output project, you can use these key project milestones.
Month 1: Project kickoff, team formation, and stakeholder engagement.
Month 3: Completion of current state analysis, KPI development, and resource allocation.
Month 6: Implementation of process optimization initiatives.
Month 9: Completion of technology enhancements and workforce training.
Month 12: Final evaluation and project closure.
Track and Achieve Manufacturing Goals
Optimise your project milestones with our Digital Transformation Starter Kit. Download now to efficiently monitor and enhance manufacturing output.
Final Thoughts
By following this structured project plan, your factory can effectively increase production output over the next 12 months.
Implementing these strategic initiatives will help you achieve significant gains and sustain long-term success in your manufacturing operations.
Embrace these strategies to unlock the full potential of your manufacturing processes, drive efficiency, and enhance productivity.
Let’s Talk Tascus
Want to see how Tascus can cut errors,
speed up production, and simplify
compliance in your factory?