How Digital Tools are Enhancing Lean Manufacturing
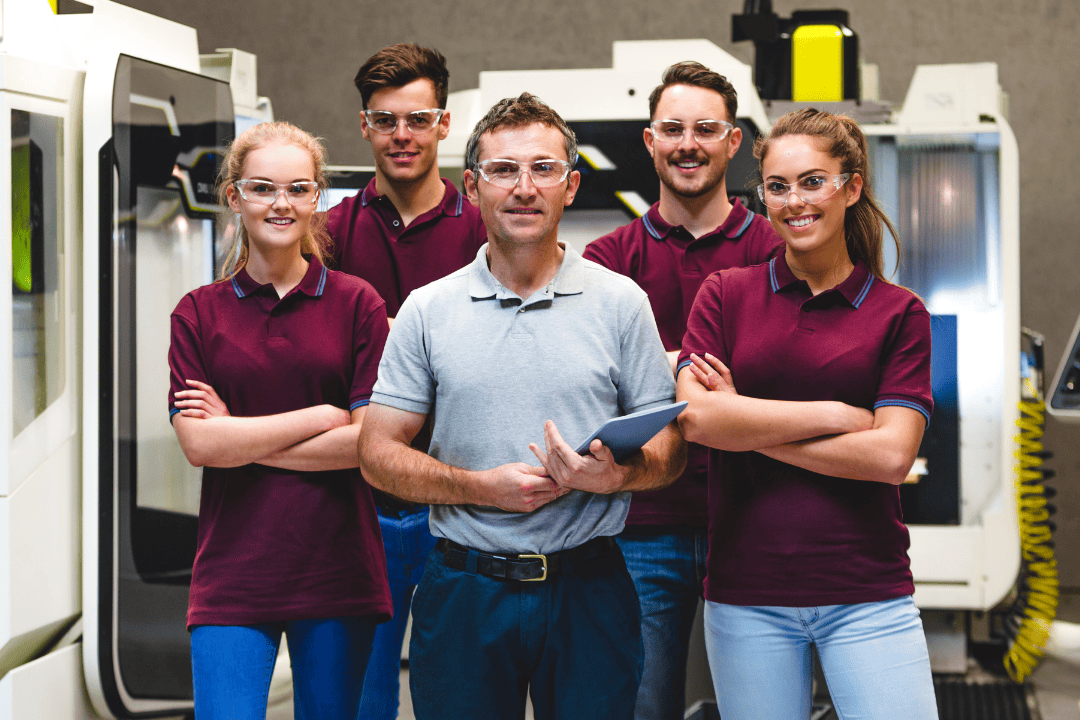
A Recap on Lean Manufacturing
Lean manufacturing is a systematic approach to production that aims to minimise waste while maximising value to the customer. Originating from the Toyota Production System, lean manufacturing focuses on creating more value with fewer resources by optimising workflows and reducing inefficiencies. The key principles of lean manufacturing are
- Value stream mapping, which identifies all the steps in a production process to eliminate non-value-added activities;
- Just-in-time (JIT) production, which ensures that materials and products are produced only as needed to reduce inventory costs; and
- Continuous improvement, or Kaizen, which encourages ongoing efforts to enhance all aspects of production through small, incremental changes.
Using these principles, lean manufacturing aims to deliver higher quality products more efficiently and at a lower cost and has significantly impacted global manufacturing by fostering efficiency, quality, and continuous improvement.
By eliminating waste, enhancing product quality, and increasing flexibility, lean principles have enabled manufacturers worldwide to reduce costs and respond swiftly to market demands. This approach has not only improved operational performance but also empowered workforces and contributed to environmental sustainability. As lean methodologies continue to evolve and integrate with new technologies, their transformative impact on manufacturing processes and practices is set to expand further.
Let’s discuss the key ways in which digital tools can enhance the core principles of Lean Manufacturing.
Enhance Your Lean Manufacturing
Boost your lean manufacturing with our free Digital Transformation Starter Kit. Get a comprehensive guide, work instructions, and capacity planning tools to optimise your processes.
1. Enhancing Value Stream Mapping
with Digital Tools
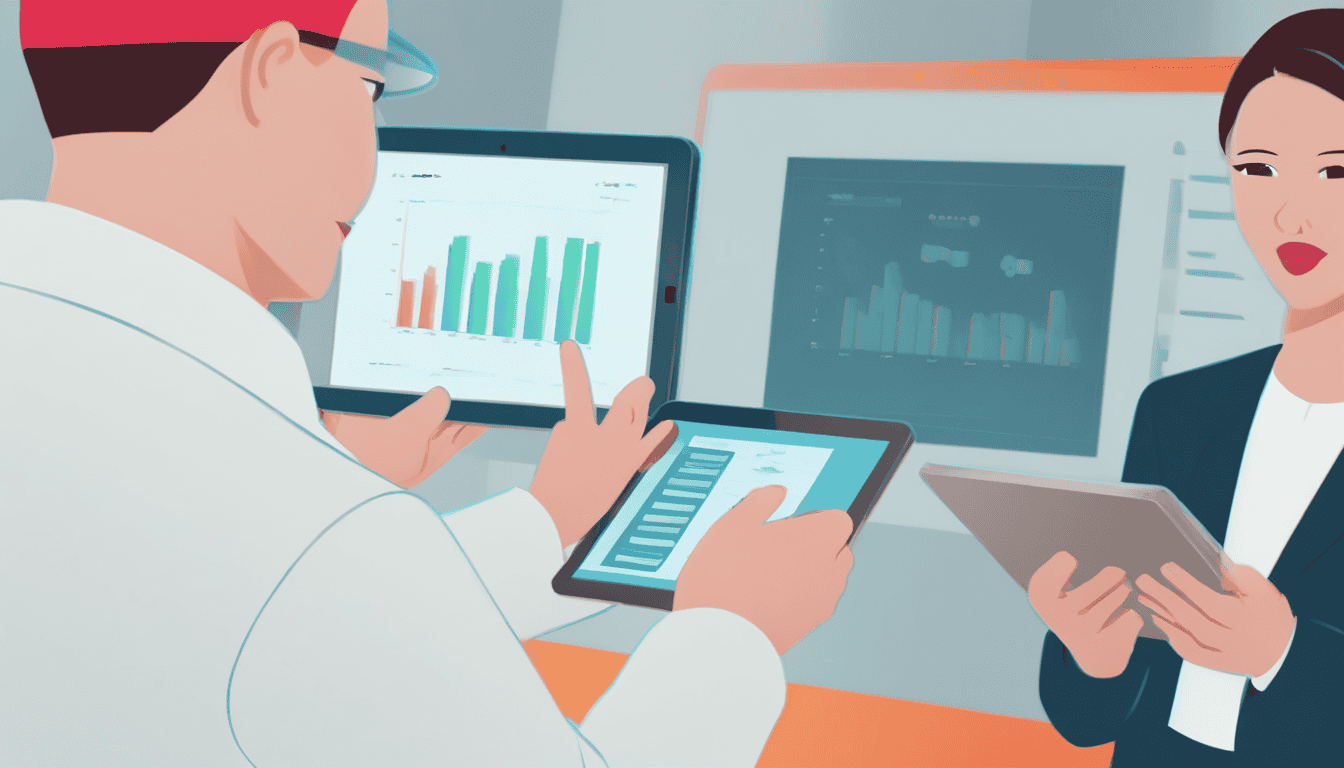
Digital tools have significantly enhanced value stream mapping by providing real-time data collection, advanced analytics, and visualisation capabilities. These tools allow manufacturers to accurately track and analyse each step of the production process, identifying inefficiencies and bottlenecks with greater precision. With digital value stream mapping, companies can create dynamic, interactive maps that are easily updated and shared across teams, facilitating better communication and collaboration. Additionally, the integration of IoT devices and sensors enables continuous monitoring and immediate feedback, allowing for quicker adjustments and continuous improvement. Overall, digital tools have made value stream mapping more precise, efficient, and effective in driving lean manufacturing initiatives.
One case study involves an automotive client who utilised our Manufacturing Execution System to track processing times on a multi-stage assembly line. By leveraging real-time data, they efficiently balanced tasks across workers on the production line, maximising output per shift. This real-time insight allowed them to quickly respond to any process changes, ensuring continuous optimisation and improved overall efficiency.
Optimise Your Value Stream Mapping
Transform your value stream mapping with our free Digital Transformation Starter Kit. Includes a comprehensive guide, work instructions, and capacity planning tools.
2. Streamlining Just-in-Time Production
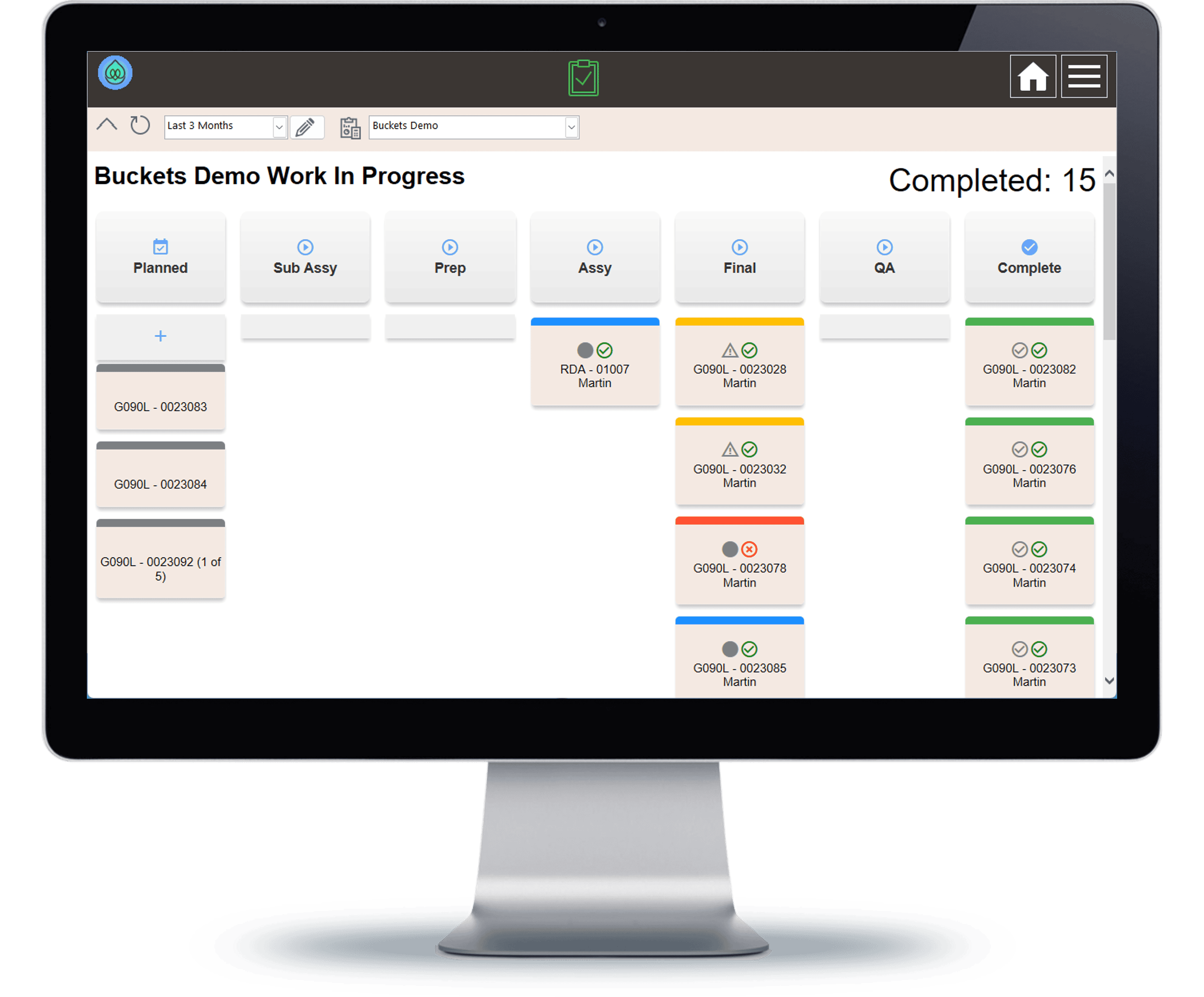
Screenshot from our Award Winning MES – Tascus
Digital tools have greatly improved just-in-time (JIT) production by enabling real-time inventory management, predictive analytics, and automated supply chain coordination.
With the integration of IoT devices, manufacturers can monitor inventory levels and production needs in real-time, ensuring that materials are ordered and delivered precisely when needed.
Predictive analytics help forecast demand more accurately, reducing the risk of overproduction and stockouts.
Additionally, automated systems streamline communication and coordination with suppliers, minimising lead times and ensuring a smooth flow of materials. These digital advancements have made JIT production more efficient, responsive, and reliable, ultimately reducing costs and improving overall productivity.
One of our clients uses real-time populated product tracking boards, automatically updated from sensors and shop floor data collection software, to monitor item progress through the factory. This system sends automated notifications and uploads product data to their client as each work order is fulfilled. This approach ensures accurate, up-to-the-minute tracking, enhances transparency with clients, reduces manual reporting errors, and improves overall communication and customer satisfaction. By automating these processes, the client has also freed up valuable employee time, allowing for greater focus on quality and productivity.
Improve Your JIT Production
Enhance your just-in-time production with our free Digital Transformation Starter Kit. Get a detailed guide, work instructions, and capacity planning tools to streamline your operations.
3. Promoting Continuous Improvement
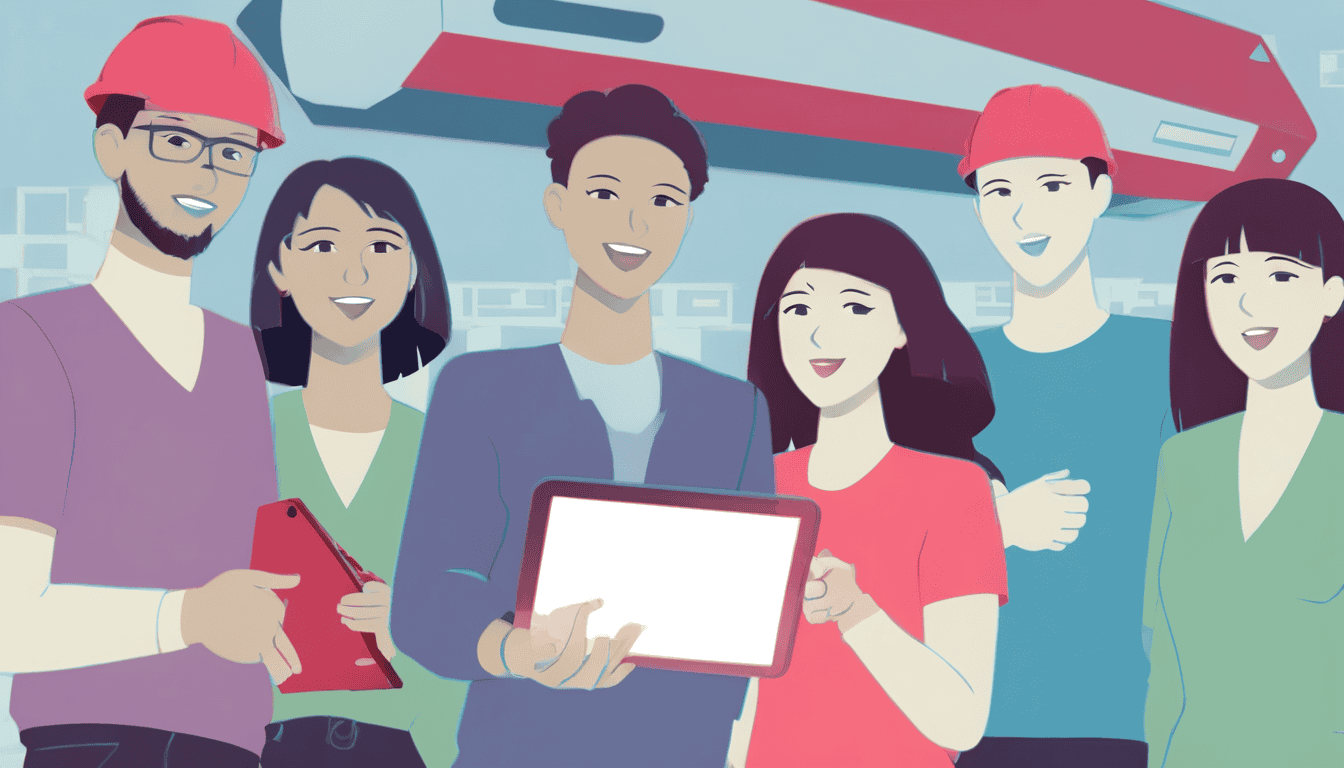
Digital tools have significantly enhanced continuous improvement (Kaizen) in manufacturing by providing real-time data, advanced analytics, and collaborative tools.
With the use of AI and machine learning, manufacturers can identify patterns and predict potential issues, allowing for proactive problem-solving and process optimization.
Real-time feedback loops enable immediate adjustments and iterative enhancements, fostering a culture of continuous improvement.
Digital collaboration tools facilitate better communication and idea-sharing among team members, encouraging collective problem-solving and innovation.
Overall, these tools empower employees to contribute more effectively to continuous improvement efforts, leading to more sustained and impactful enhancements in manufacturing processes.
Our Manufacturing Execution System (MES), Tascus, provides access to real-time data that clients use to prioritize continuous improvement efforts. For example, a dashboard displays the largest variances between actual production times and standard times by product type. Continuous Improvement teams can then focus on these high-variance products to identify and address underlying issues in the manufacturing process. This targeted approach enables more effective problem-solving, leading to enhanced efficiency, reduced waste, and improved production consistency.
Boost Continuous Improvement
Drive continuous improvement with our free Digital Transformation Starter Kit. Access a detailed guide, work instructions, and capacity planning tools to optimise your processes.
4. Reducing Waste with Precision and Efficiency
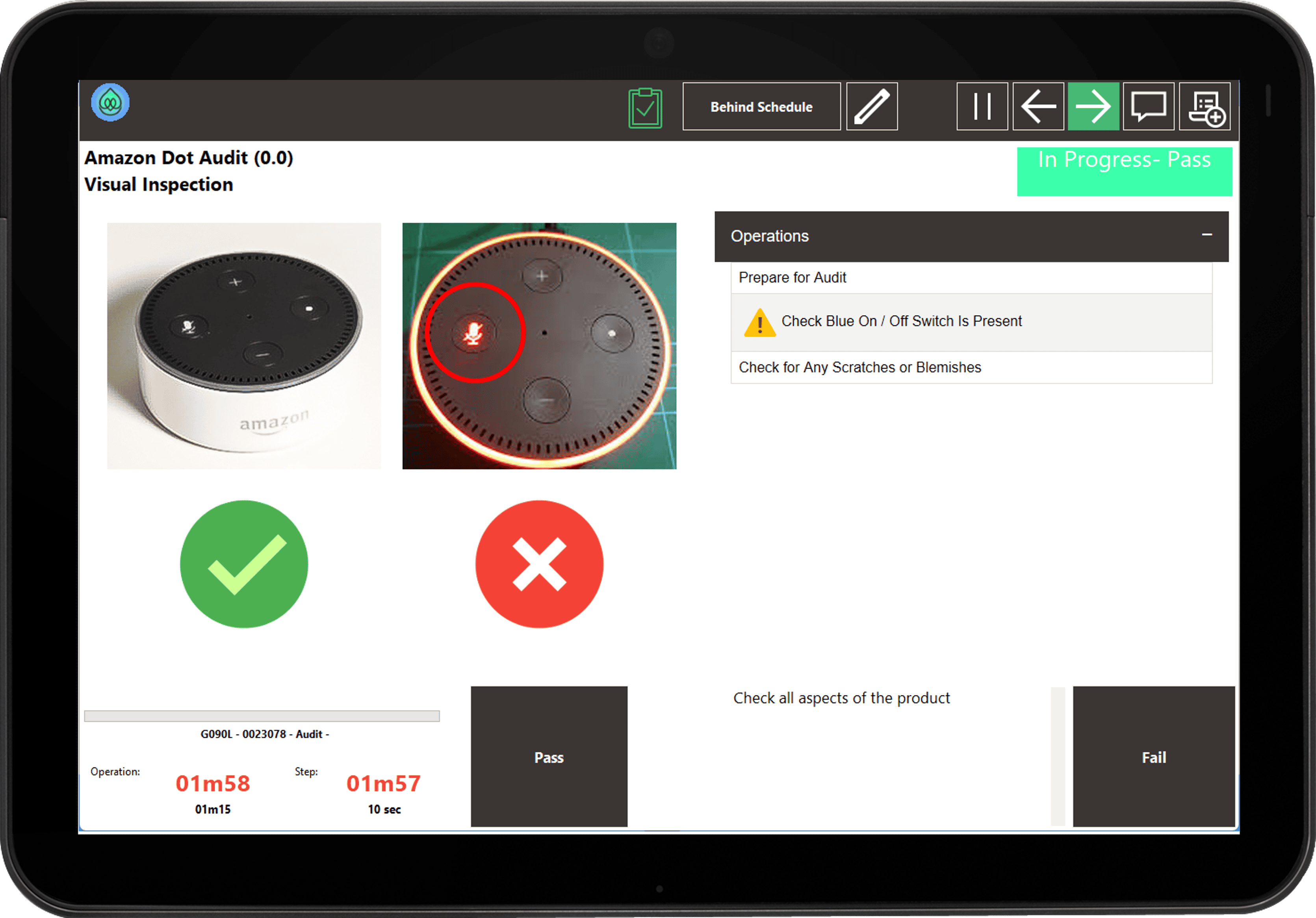
Screenshot from our Award Winning MES – Tascus
Digital tools help identify and reduce waste in manufacturing by providing detailed insights and advanced analytics that highlight inefficiencies and areas for improvement.
With real-time data collection from IoT sensors and shop floor data collection software manufacturers can monitor every aspect of the production process, from raw material usage to energy consumption and machine performance.
Analytics can pinpoint sources of waste, such as excessive inventory, unnecessary motion, defects, overproduction, waiting times, and inefficient processes.
Automated quality control systems can detect defects early in the production process, reducing rework and scrap.
A client achieved an 80% reduction in rework by integrating simple quality control steps early in their process, performed by assembly operators rather than relying solely on end-of-line testers or quality inspectors. This proactive approach helps ensure issues are detected and addressed promptly, promoting a “build right first time” philosophy. As a result, the client has significantly improved product quality and efficiency, reducing waste and costs associated with rework.
Finally, Predictive maintenance tools monitor equipment health and predict failures before they occur, minimising downtime and extending machine life.
By leveraging these digital tools, manufacturers can implement targeted strategies to eliminate waste, enhance efficiency, and improve overall productivity, aligning with lean manufacturing principles and driving continuous improvement.
Minimise Waste Effectively
Eliminate waste with our free Digital Transformation Starter Kit. Get a comprehensive guide, work instructions, and capacity planning tools to enhance efficiency and reduce costs.
Final Thoughts
The integration of digital manufacturing tools has significantly enhanced lean manufacturing practices, driving efficiency, quality, and continuous improvement across the industry.
From value stream mapping to just-in-time production, continuous improvement initiatives, and waste reduction, digital tools provide the real-time data and advanced analytics necessary to optimize every aspect of the manufacturing process.
These technologies not only empower manufacturers to respond swiftly to changes and challenges but also enable a proactive approach to quality control and process enhancement.
As digital tools continue to evolve, their role in transforming lean manufacturing will only become more vital, ensuring that manufacturers remain competitive and innovative in a rapidly changing market.
Let’s Talk Tascus
Want to see how Tascus can cut errors,
speed up production, and simplify
compliance in your factory?