Improving Manufacturing Quality: 5 Simple Steps for 2024
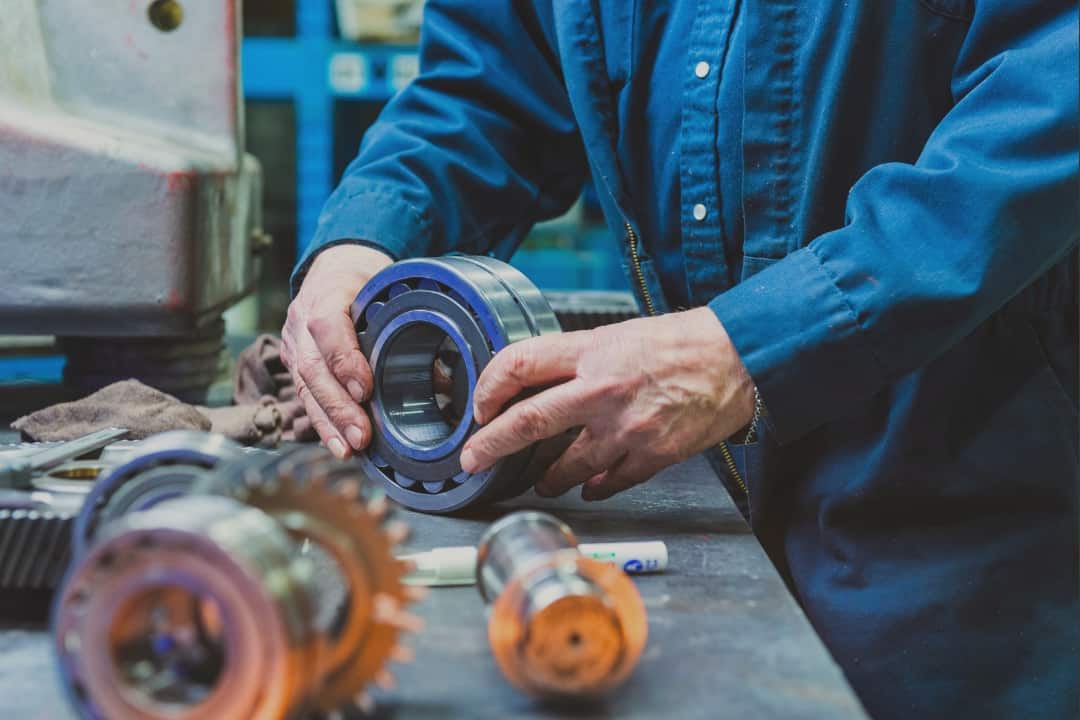
Introduction
In manufacturing, product quality is key to customer loyalty, reputation, and profitability. However, maintaining high quality is challenging due to variable raw materials, complex processes, and manual checks. These challenges are even greater when balancing speed and cost-efficiency. Defects, rework, and non-compliance can significantly impact your bottom line and brand.
This blog post presents “Improving Manufacturing Quality: 5 Simple Steps for 2024.” We will offer practical strategies to enhance your quality control measures. These steps require effort and vigilance but provide a strong foundation for a robust quality management system.
Stay with us until the end to learn how modern solutions can simplify these processes, making quality management more manageable and effective.
Step 1: Implement Real-Time Monitoring
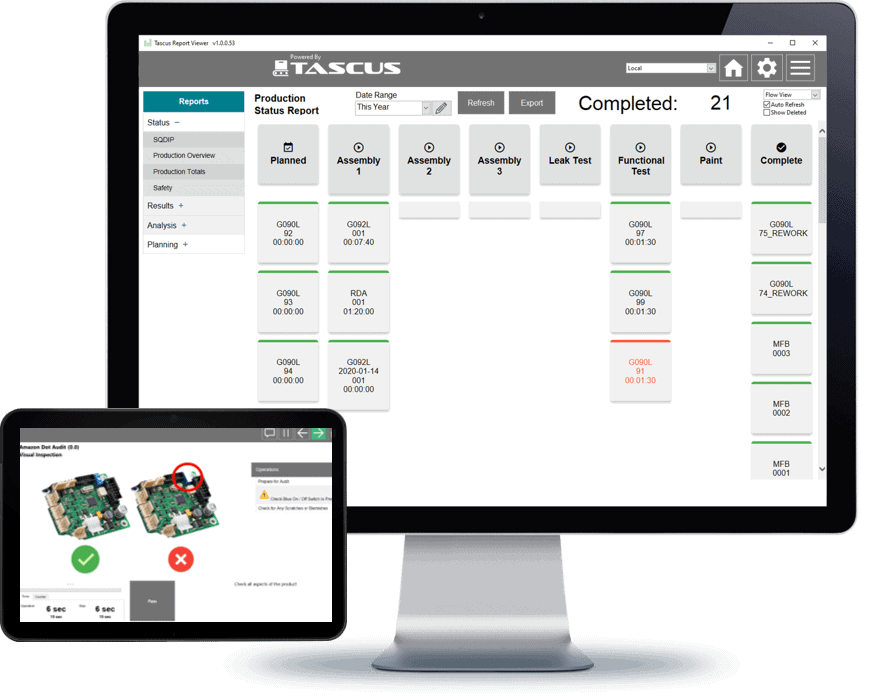
Screenshot Award Winning MES – Tascus.
The Value of Real-Time Insights
On a busy manufacturing floor, having real-time visibility into your processes is invaluable. It helps identify areas for quality improvement and ensures smooth operations. Real-time monitoring doesn’t have to involve complex systems or high costs.
Starting Simple with Accessible Tools
Begin with simple, accessible tools. For small to medium-sized businesses, using basic software solutions can provide essential insights without overwhelming you with data or stretching your budget. These solutions can track production metrics, monitor machine performance, and alert you to issues before they escalate.
Using spreadsheets can also be an effective way to monitor your processes. Manually recording key metrics such as production volumes, times, and error rates provides a solid foundation for understanding your operations and identifying trends over time. This approach offers immediate insights and lays the groundwork for adopting more advanced digital solutions as your business grows and your needs evolve.
Laying the Groundwork for Future Advancements
Starting with straightforward methods offers two main benefits. First, it provides immediate insights into your processes, allowing quick, informed decisions. Second, it prepares you for a seamless transition to advanced monitoring systems as your needs grow.
Implementing real-time monitoring is a crucial first step towards improving manufacturing quality. By starting simple, you build a scalable, data-driven foundation for your business’s future growth.
Optimise Your Manufacturing Processes
Download our free Starter Kit for an actionable guide, work instruction template, and capacity planning tools to enhance your manufacturing operations.
Step 2: Establish Clear Quality Standards
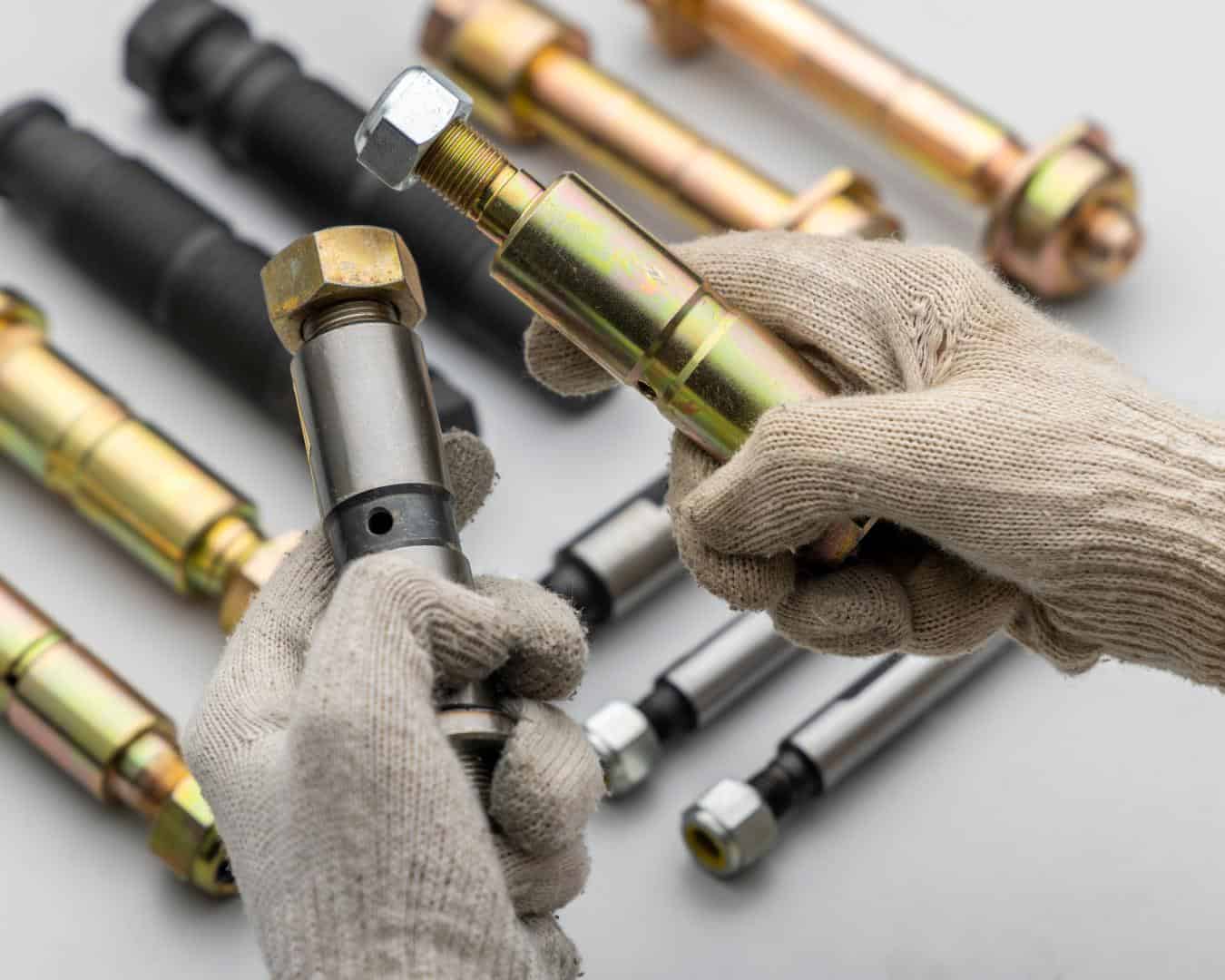
The Importance of Defining Quality
Setting clear quality benchmarks in your manufacturing operations is crucial. Establishing quality standards isn’t just about compliance; it’s about fostering a culture of excellence.
Leveraging Existing Resources
Improving manufacturing quality doesn’t mean starting from scratch. Utilize your existing resources—historical production data, customer feedback, and your team’s expertise—to define and enhance what high quality means for your business.
Crafting Your Quality Standards
Gather your team and review the quality aspects that matter most to your customers and the integrity of your products. Draft quality standards that are ambitious yet achievable, covering everything from material specifications to final product inspections.
Documenting and Communicating Standards
Effective documentation and communication are key. Use physical checklists or digital manuals to ensure standards are clear and accessible to all team members. This shared commitment to quality fosters a culture of continuous improvement.
Utilizing Templates and Frameworks for Efficiency
Templates and frameworks can streamline the process. Quality control checklists and frameworks for documenting product specifications can be adapted to fit your needs, making it easier to establish and maintain quality standards.
Interested in streamlining your quality standards? Our Digital Transformation Starter Kit, including a versatile Capacity Planning Template, is designed to enhance operational efficiency. Explore the Starter Kit here and take the first step towards seamlessly integrating quality into your manufacturing processes.
Step 3: Train and Empower Your Team
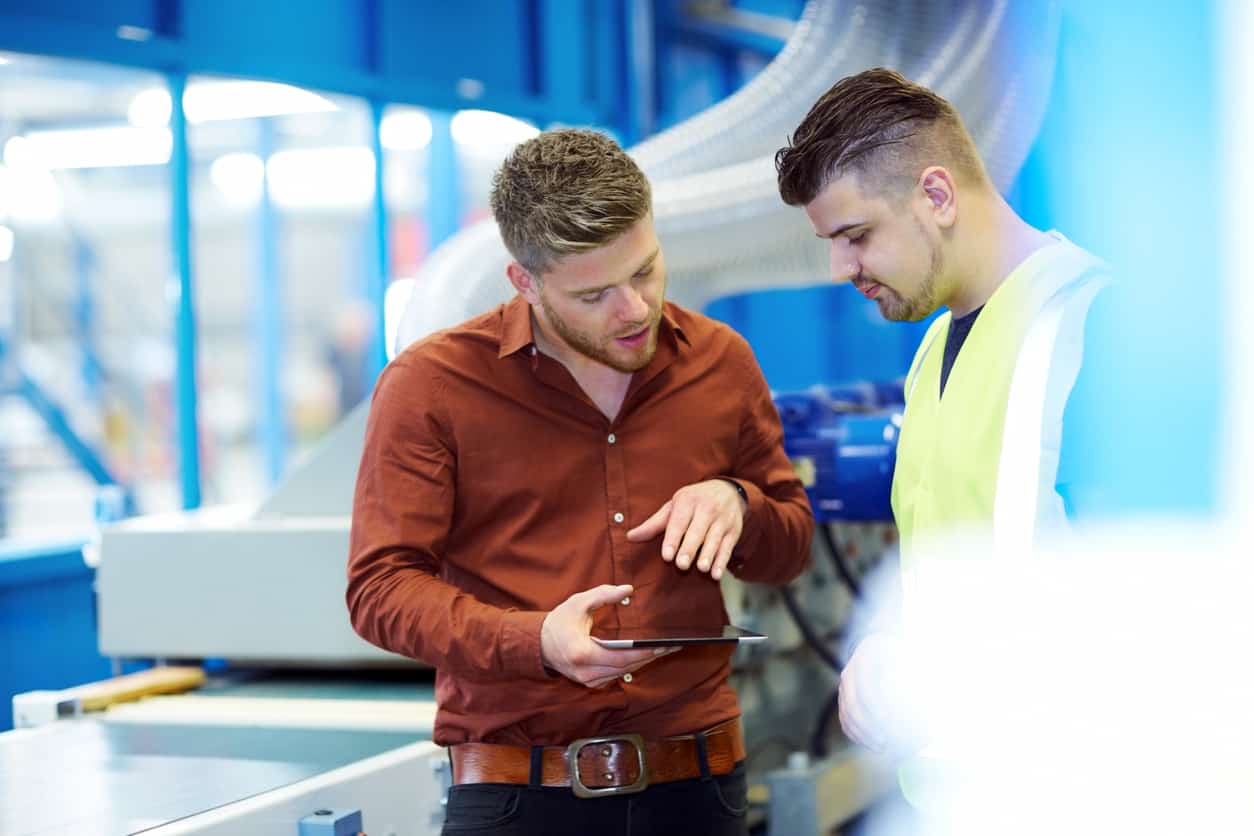
Improving manufacturing quality is a team effort, where every member plays a crucial role. Equipping your team with the right knowledge and tools not only empowers them but also fosters a shared sense of responsibility towards maintaining high standards. Training is more than a procedural task; it’s an investment in your team’s growth and your business’s future.
Embracing Continuous Learning
Manufacturing processes and technologies evolve rapidly. A culture of continuous learning ensures your team remains agile and ready to adapt and implement the best practices in quality control. Regular training sessions that focus on the ‘why’ behind each process, not just the ‘what’, can spark curiosity and engagement.
Leveraging Work Instructions
Clear, concise work instructions are one of the most effective tools at your disposal. They help standardise processes, minimise errors, and ensure consistency in product quality. Effective work instructions go beyond documenting steps; they should be easily understood and accessible to all team members, regardless of their role or experience level.
Promoting Ownership and Accountability
When team members understand the impact of their work on product quality, they are more likely to take ownership and pride in their contributions. Encourage this mindset by involving them in creating work instructions, problem-solving, and decision-making processes. Recognising and celebrating achievements in quality improvements can further reinforce their commitment to excellence.
By investing in your team’s training and empowerment, you’re not just enhancing product quality; you’re building a strong, cohesive unit aligned with your business’s values and goals. Starting with the right resources can make this journey smoother and more effective.
Free Download
Work Instructions Template
Download our free Digital Transformation Starter Kit. This includes a guide, video and spreadsheet to create excellent work instructions.
Step 4: Utilise Data for Continuous Improvement
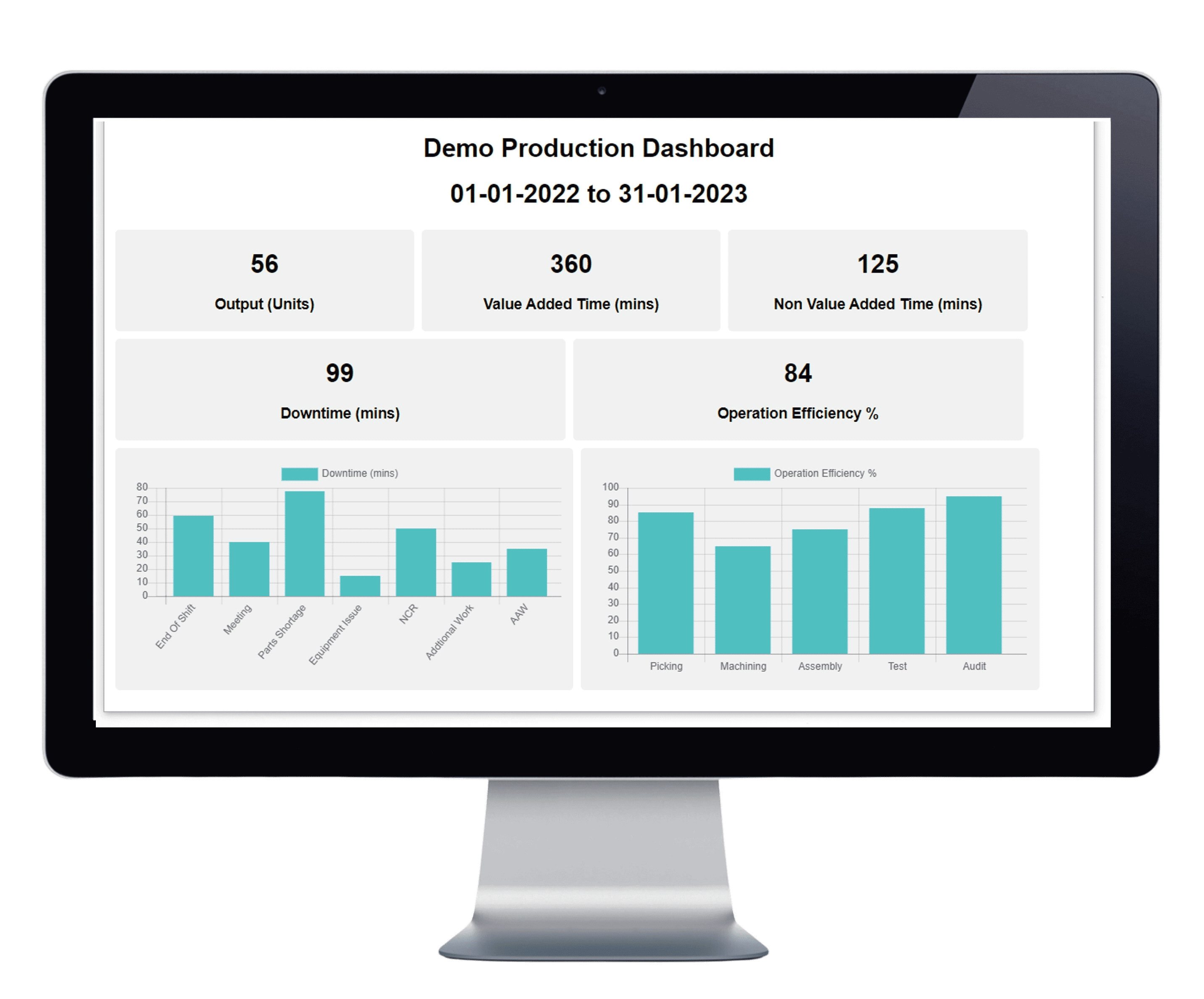
Screenshot Award Winning MES – Tascus.
In modern manufacturing, data is crucial for identifying both successes and areas for improvement. Collected throughout your production processes, this information helps guide continuous improvement. The real value of data lies in its effective analysis and application.
Turning Data into Actionable Insights
Data such as throughput rates, operational times, and quality control outcomes can significantly improve your manufacturing processes. By examining performance indicators, you can identify trends, inefficiencies, and strategies for improvement. This ensures your decisions are based on solid evidence, leading to sustainable advancements.
Simplifying Data Analysis
Data analysis might seem daunting for those unfamiliar with statistics. However, there are many tools available that simplify the process, making it accessible to everyone. Using straightforward analytical tools and intuitive software, you can convert complex data sets into clear, actionable insights, empowering your team to make informed decisions.
Fostering a Culture of Continuous Improvement
Encourage your team to regularly engage with data, fostering curiosity and innovative solutions. This approach maximises the value of your insights and reinforces quality and efficiency as core principles of your operations.
Leveraging data for continuous improvement involves a proactive approach, anticipating potential issues and aiming for excellence. In today’s data-driven world, let data guide your manufacturing processes to achieve high quality and operational efficiency.
💡Remember, data is more than just numbers; it’s a powerful tool to enhance your manufacturing process. Embrace it fully to drive excellence and innovation.
Step 5: Foster a Quality-centric Culture
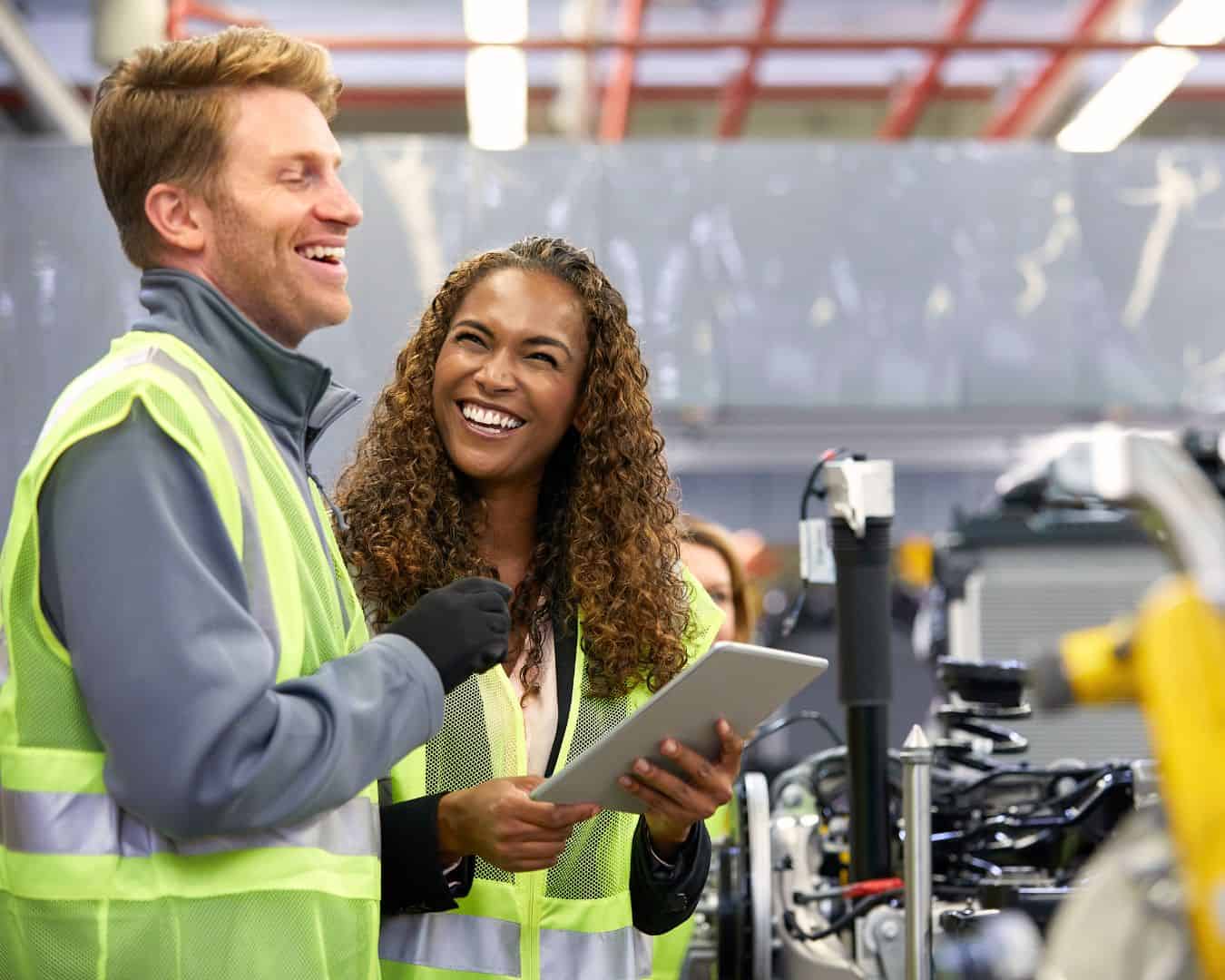
Foster a Culture of Excellence
Get the essential guide, templates, and tools to build a quality-centric culture, empowering your team to drive excellence at every stage.
Conclusion: Your Path to Quality Excellence with Tascus MES
Improving manufacturing quality doesn’t have to be complex. The steps outlined above provide a roadmap to achieving higher standards of quality, efficiency, and customer satisfaction. But what if you could integrate all these steps into a single, seamless solution? That’s where our Manufacturing Execution System, Tascus, comes in.
Tascus empowers your manufacturing operation with real-time monitoring, quality standards management, employee training tools, data analytics for continuous improvement, and fostering a quality-focused culture. By centralising these functions, Tascus streamlines your path to product excellence, making it easier to implement the changes that matter most.
Interested in seeing Tascus in action?
Experience how Tascus can transform your production line and elevate your productivity. Book a call with us today and take the first step towards a future where efficiency, quality, and innovation are guaranteed.
Let’s Talk Tascus
Want to see how Tascus can cut errors,
speed up production, and simplify
compliance in your factory?