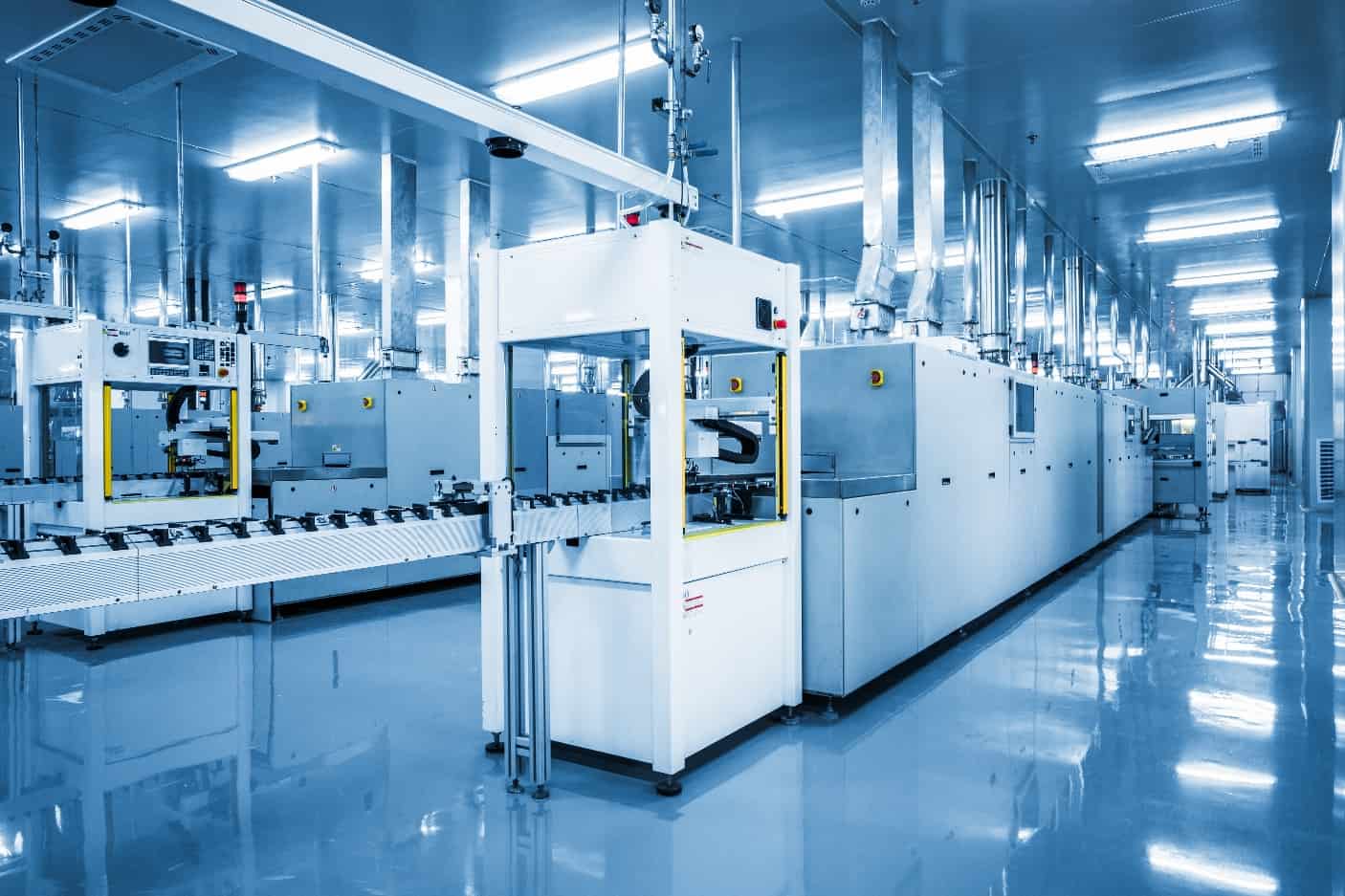
5 Ways to Increase Manufacturing Productivity with an MES
In order to remain competitive, manufacturers need to maintain high manufacturing productivity – or high revenue generated per employee.
Most methods of improving manufacturing productivity begin with a thorough analysis of a company’s systems and manufacturing processes, to eliminate waste and optimise the value-adding processes.
- Eliminate wasteful processes.
- Systemise what’s left.
- Automate wherever possible.
When it comes to automating processes, a Manufacturing Execution System (MES) can help. A good MES can automate the manual decision making, data collection and process instructions, that have previously been paper-driven or controlled using a variety of separate IT systems.
Here are our top 5 tips on how an MES can be used to make the biggest impact on manufacturing productivity and company profits:
Reduce Labour Costs
Manual assembly, test and inspection processes can be very time consuming, particularly when manufacturing complex products. Traditional paper-based work instructions or those displayed in basic image viewing software can limit the flexibility of training new operators. It can also slow down complex labour-intensive manufacturing processes.
Work instruction displays in an MES will reduce the time spent in manufacture, by making it faster to train operators proficiently. When an MES is used to display videos of complex assembly processes or exploded views that illustrate the details of the manufacturing process, operators can get up to speed much quicker.
Digital work instructions in an MES can reduce labour costs.
Digital work instructions can also be used to speed up labour-intensive assembly processes, by reducing the amount of context switching that operators have to do. An operator can identify the product they are building and rely on the MES to display the correct work instructions for them. They do not need to waste time looking for the correct version of a work instruction.
Reduce Material Costs
Material costs can be reduced by improving the accuracy and repeatability of manufacturing processes. By integrating an MES with existing shop floor equipment or using a statistical process control (SPC) module within the MES, a production control step can be used to monitor, control and adjust process parameters. When the accuracy and repeatability of processes are improved there will be less material wastage through scrap or rework.
Reduce Defects & Errors
Reducing defects and errors in the manufacturing process can have a huge impact on productivity and profitability. It avoids wasting materials and labour on non-value adding processes. An MES helps by adding quality checks to the manufacturing process so errors are detected or prevented early on. This ensures that defects leading to lengthy and expensive rework do not appear at the end of manufacturing.
A common example seen by manufacturers is a component fitted in error at an early assembly process. The product goes on to have several manufacturing processes completed and is functionally tested before being shipped to the customer. If the defect is detected at a final functional test, the product must be completely stripped down so that the component can be replaced. This can often take up to 5 times the standard production time.
Using a quality control step in an MES to ensure correct components are assembled.
When a manufacturer uses an MES with quality checking steps, this error could be detected at the time of assembly. The operator would be notified that this was an incorrect component and could remedy the error immediately, with minimal impact on time.
Reduce Cycle Times
When cycle times can be reduced, a manufacturer can output more product in each shift. This enables them to generate more revenue from their factory every month.
An MES can be used to reduce cycles times by using it to automate manufacturing processes. This means that previously manual processes can be run unattended. One of our clients used this method to reduce their cycle times by 25% and increased their shift output. They had one operator performing as an assembly process, then a functional test. We created a customised production step in our MES for their functional test so that the operator could perform an assembly, then start an automated test and return to assembling the next product.
Improve Delivery Performance
Improving delivery performance by reducing production lead times, means a manufacturer can generate more revenue from increased product sales.
One of our clients, Mettler Toledo Safeline, found that their existing paper-driven production process had several stages where the product was left in batches waiting for an inspection or test process. When they used our MES they eliminated waiting times and as a result, reduced their production lead time by 50%.
Unleash the Power of Digital Manufacturing
Download our free Digital Transformation Starter Kit to set the gold standard for operational clarity and excellence.