Cost-Effective Traceability Solutions for Manufacturers
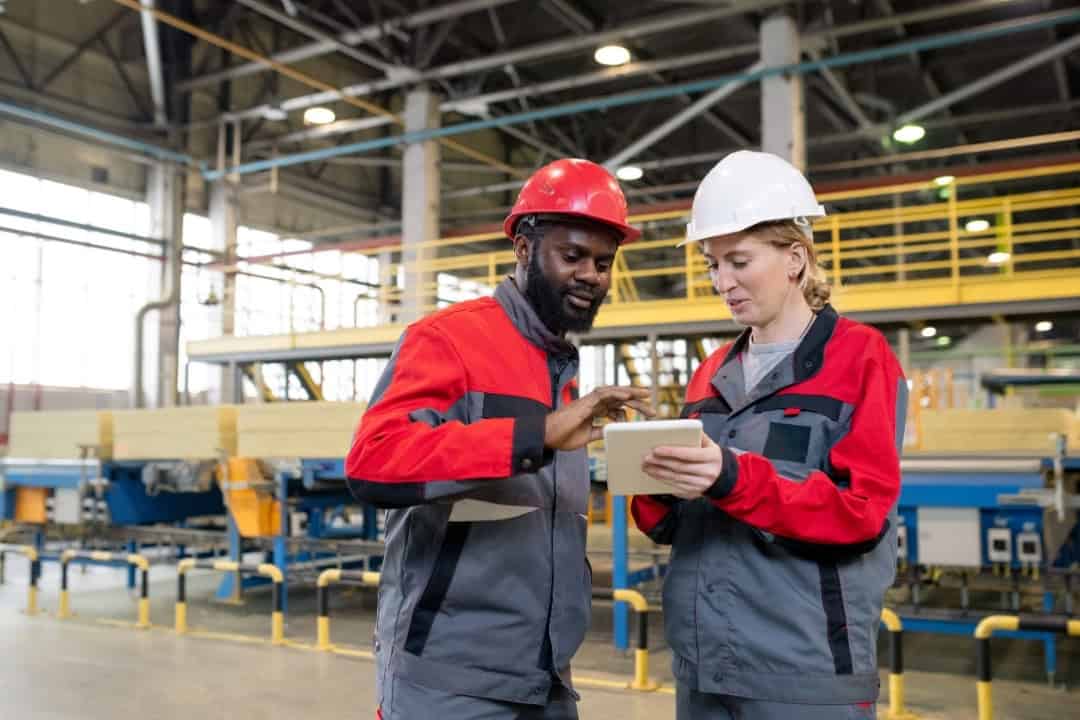
Introduction
In manufacturing, traceability means monitoring the journey of a product from the sourcing of raw materials, through the production process, and finally to the distribution and delivery to the end customer. This detailed tracking allows manufacturers to maintain comprehensive records that can be used to verify the quality and safety of their products.
Understanding Traceability
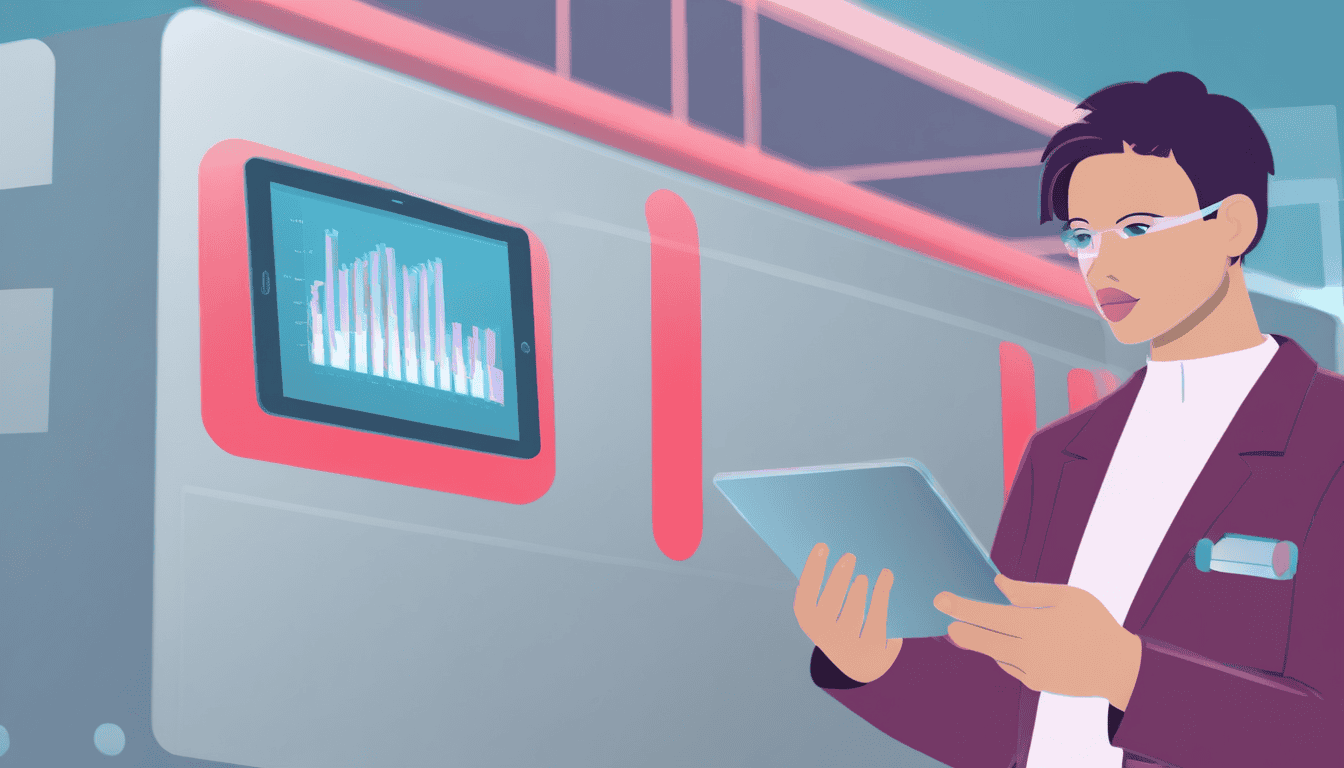
Traceability is more than just a regulatory requirement; it is a strategic tool that offers many benefits to manufacturers. Traceability can significantly reduce costs in manufacturing through better quality control and fewer recalls. By continuously monitoring and recording every step of the production process, manufacturers can identify potential quality issues early, preventing defects from escalating into larger problems. This proactive approach reduces costs associated with scrap, rework, and production downtime.
Additionally, in the event of a defect, traceability allows for precise identification of affected batches, leading to targeted recalls rather than broad, costly ones. This minimizes the financial impact and preserves the brand’s reputation.
Traceability also facilitates regulatory compliance by providing the necessary documentation for industry standards. Additionally, it boosts customer confidence by offering transparency about product origins and safety, thereby building trust in the brand.
Overall, effective traceability streamlines operations, enhances product quality, and reduces the likelihood and cost of recalls.
Boost Traceability
Enhance traceability with our free Digital Transformation Starter Kit. Get tools to monitor production, improve quality control, and ensure compliance.
Cost Benefits of Traceability
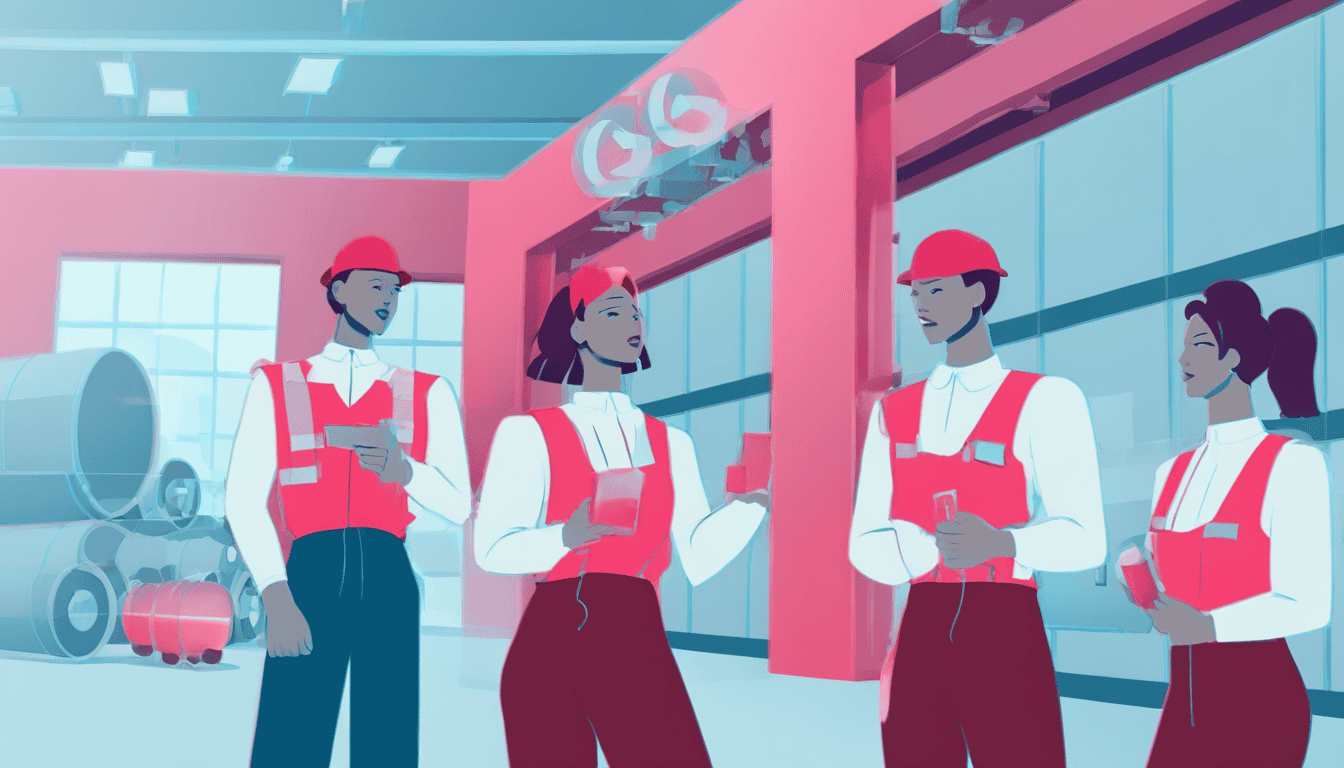
There are 2 main areas in which traceability leads to costs savings – traceability leads to improved quality control, savings from less rework and recalls.
Traceability Improves Quality Control
Real-time monitoring and early issue detection are pivotal components of traceability that enhance quality control in manufacturing. By continuously tracking every stage of the production process, manufacturers gain immediate visibility into the operations, allowing them to swiftly identify any deviations or anomalies. This instant detection enables prompt corrective actions, preventing minor issues from escalating into significant defects. As a result, manufacturers can ensure that only products meeting the highest quality standards proceed through the production line, thereby reducing the need for costly rework and minimizing production downtime. This proactive approach not only maintains product quality but also optimizes operational efficiency, ultimately leading to substantial cost savings.
Protection of brand reputation and customer trust
Traceability contributes to significant cost savings from fewer product recalls by allowing manufacturers to precisely identify and isolate defective products. When a defect is detected, a robust traceability system can quickly pinpoint the specific batches affected, enabling targeted recalls instead of extensive, costly ones. This precision reduces the volume of products that need to be withdrawn from the market, cutting down on recall-related expenses such as logistics, replacements, and customer compensation.
Additionally, the ability to efficiently manage recalls protects the brand’s reputation by demonstrating a commitment to quality and accountability.
Traceability enhances transparency and reliability, fostering customer confidence in the safety and quality of products. This trust not only safeguards current sales but also attracts new customers, ensuring financial health and growth of the company.
Enhance Quality Control with Traceability
Start your journey to better traceability with our free Digital Transformation Starter Kit. Get guides and templates to introduce real-time monitoring and improve quality control.
Implementing Traceability
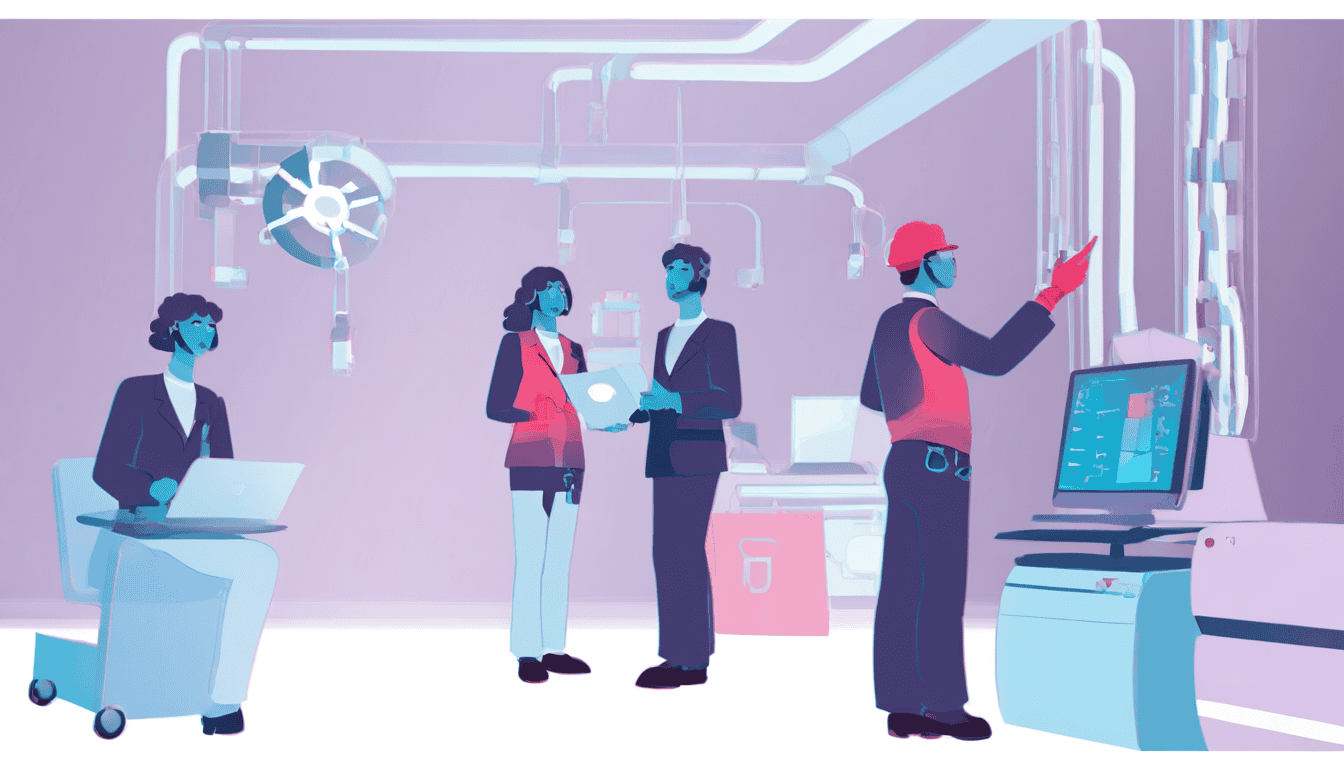
Map the Production Process
When implementing traceability in manufacturing, first, it’s essential to map out the entire production process, identifying all critical points where data needs to be collected and tracked. This includes sourcing of raw materials, various stages of production, and the final distribution of products.
Select Technologies
Next, it’s important to select the appropriate technology.
While traceability can be implemented with paper and spreadsheets, this approach comes with significant limitations and challenges compared to using digital tools and software. Manual systems relying on paper records and spreadsheets are prone to human error, time-consuming data entry, and difficulties in maintaining consistent and accurate records.
Digital tools and software can simplifying the traceability process by automating the collection, management, and analysis of data throughout the production lifecycle, significantly reducing the manual effort and potential for errors.
Systems like ERP (Enterprise Resource Planning) and MES (Manufacturing Execution Systems) can be used to ensure seamless data flow across all stages of production. This integration allows for real-time monitoring and immediate access to critical information, enabling quick identification and resolution of any quality issues.
Barcoding and RFID (Radio-Frequency Identification) systems are examples of digital tools that streamline the tracking of materials and products. These tools provide precise and instantaneous data capture, which is then stored in a centralized system.
Design Data Collection Protocols
Establishing clear protocols for data collection, storage, and retrieval ensures that information is accurate and readily available when needed. Regular audits and updates to the traceability system help maintain its effectiveness and adapt to any changes in the production process or regulatory requirements.
Start Mapping Your Production Process
Begin your traceability journey with our free Digital Transformation Starter Kit. Get guides and templates to map your production process and select the right technologies.
Final Thoughts
By carefully planning and considering these factors, manufacturers can create a comprehensive traceability system that enhances quality control, reduces costs, and improves overall operational efficiency.
Let’s Talk Tascus
Want to see how Tascus can cut errors,
speed up production, and simplify
compliance in your factory?