The Ultimate Guide to Manufacturing Execution Systems in 2023
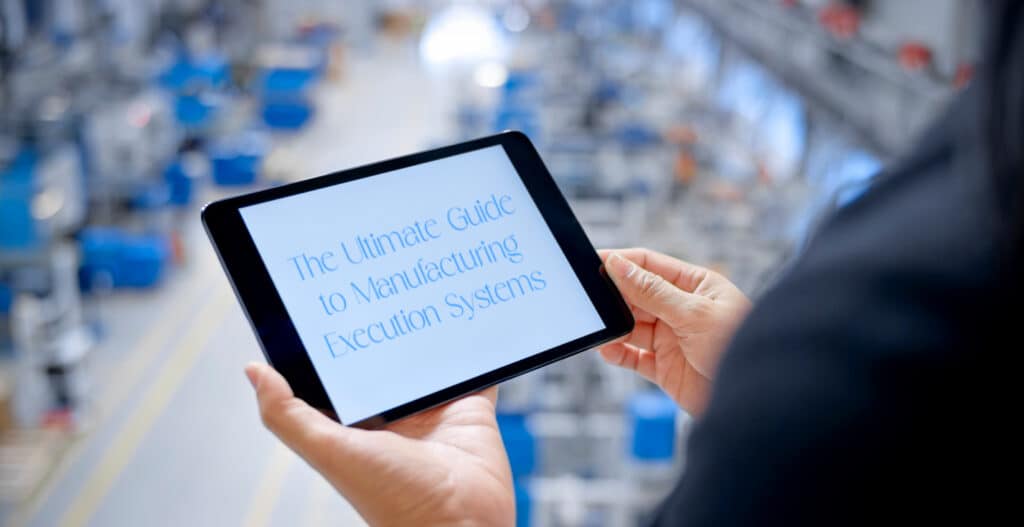
How Does a Manufacturing Execution System Work?
A MES helps guide production operators step by step, through all the tasks required to transform raw materials into finished goods. It does this using digital work instructions, production routings and connecting to production machinery to build a traceable record of the manufacture of products within a factory.
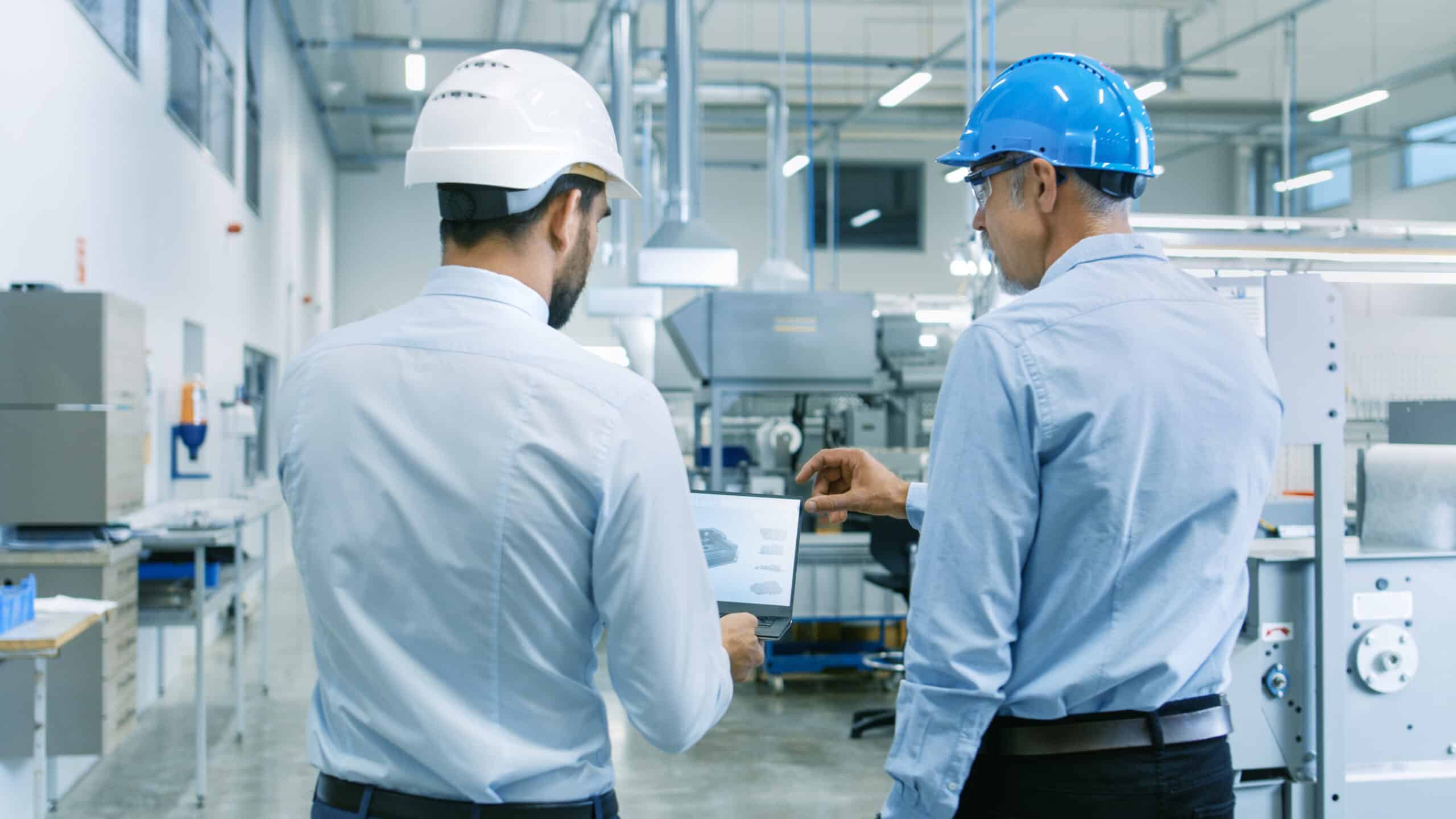
Unleash the Power of Digital Manufacturing in 5 Steps
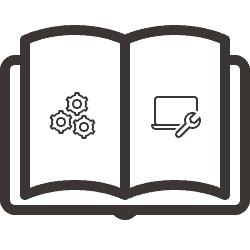
In this article, I will explain what a Manufacturing Execution System is and take you through the stages required to set up and implement an MES in your manufacturing organisation.
Overview
We are currently experiencing the 4th Industrial Revolution. Machines and manual operations are being connected, bringing the benefits of automation to entire production processes and factories.
A Manufacturing Execution System is one way to implement Industry 4.0 into a business. It helps manufacturing companies to remain competitive and relevant in the future. Business leaders recognise that manufacturers can’t compete with low-cost manufacturing, so they must develop new and innovative manufacturing techniques.
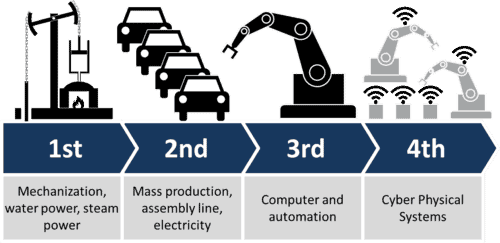
An overview of the 4 Industrial Revolutions (Source: Wikipedia)
What is a Manufacturing Execution System?
Every person working in the manufacturing industry knows just how complicated all the processes can get. From sales to invoicing, work orders, manufacturing, and beyond, every manufacturing step has its own individual process. This collection of the processes, however, needs to work in unison to ensure a smooth overall manufacturing process.
There’s quite a big difference between being a technician and being an accountant. This makes it difficult for all parties to manually communicate and record each piece of data. What happens when all these processes are out of sync? Even the slightest error or miscommunication can throw an entire process off. This means there needs to be an effective way of managing and controlling the manufacturing process.
That’s where a Manufacturing Execution System (MES) comes in. By effectively digitalizing data collection and controlling the entire system from one platform, a MES can help make manufacturing processes more efficient and productive.
What does a manufacturing execution system do?
A Manufacturing Execution Systems’ main job is to control and track the process flow of products through a factory. From the moment a manufacturing works order is released by an order management system, for example, a financial accounting package or an MRP system, a manufacturing execution system is what takes over.
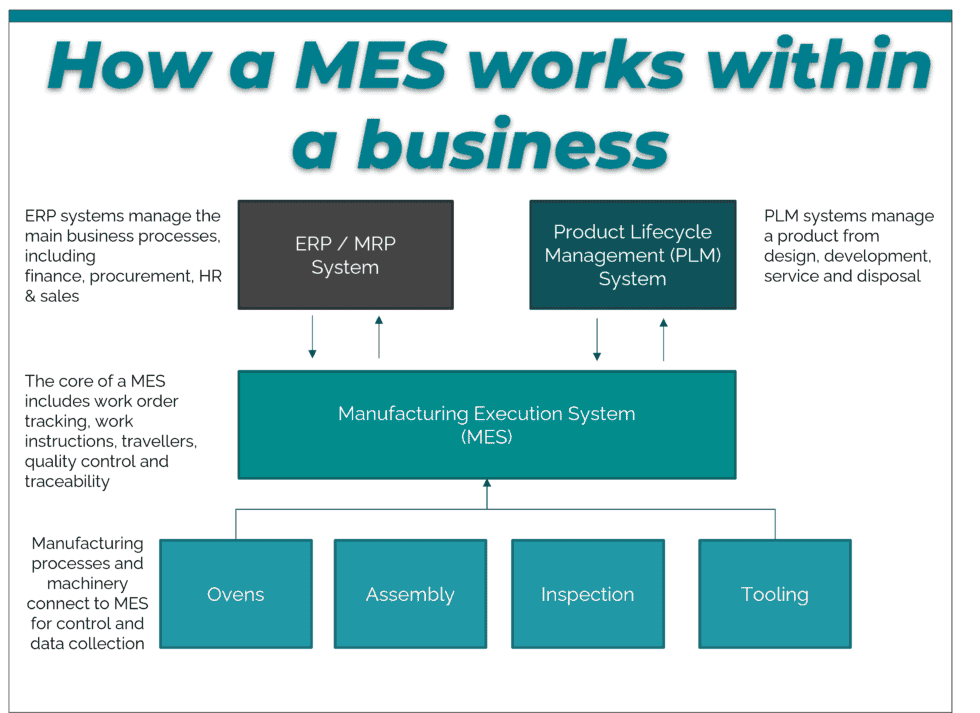
There is also a two-way communication back to those systems. The MES should guide the products from process to process, making sure they travel through the correct route. Additionally, it should capture all the data along the way, eliminating mistakes as early as possible in the process.
In simple terms, a mes replaces the paper-based manufacturing traveller you have with a product, from process to process. It’s the thread that tags processes together. It ensures that a specific manufacturing order goes through the right process, in the right order, with the right parameters. The mes should take control to make sure that all happens seamlessly, efficiently, and that data is captured immediately.
Example
You have a manufacturing process where you need put a batch of your product into an oven. For this order the product needs to go into the oven at one hundred and fifty degrees for ten hours. Previously, the information probably would have lived on the paper traveller stating – this batch in the oven, 150 degrees, 10 hours. It would mean selecting the right programme on the oven, setting the timer and clicking OK.
However, with the manufacturing execution system, when the works order for the product is at the stage of ready to go into the oven the MES should scan that data, ideally, through an industry 4.0 connection. It should then talk to the oven and select the right programme, the correct temperature and set a timer, automatically.
Additionally, it should update the work in progress for the order, onto something such as an online dashboard. For example, at the oven stage, two hours into a 10 hour process, it should update all your efficiency calculations and feed that information back to your MRP system – if it needs to go back to that for financial reporting reasons.
Example
You have a manufacturing process where you need put a batch of your product into an oven. For this order the product needs to go into the oven at one hundred and fifty degrees for ten hours. Previously, the information probably would have lived on the paper traveller stating – this batch in the oven, 150 degrees, 10 hours. It would mean selecting the right programme on the oven, setting the timer and clicking OK.
However, with the manufacturing execution system, when the works order for the product is at the stage of ready to go into the oven the MES should scan that data, ideally, through an industry 4.0 connection. It should then talk to the oven and select the right programme, the correct temperature and set a timer, automatically.
Additionally, it should update the work in progress for the order, onto something such as an online dashboard. For example, at the oven stage, two hours into a 10 hour process, it should update all your efficiency calculations and feed that information back to your MRP system – if it needs to go back to that for financial reporting reasons.
Summary
In essence, the manufacturing execution system controls the process flow, and reduces any chance of mistakes in the process. It gathers the data for every single process, who’s done it, when it was done and what the parameters were. It also gives immediate data visibility for each order, what’s in working progress and what stage it’s up to. Ultimately this will help you make more informed and better planning and reporting decisions.
Unleash the Power of Digital Manufacturing in 5 Steps
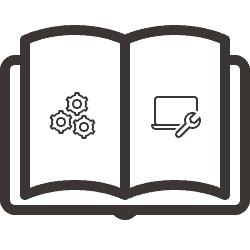
What Are The Benefits of a Manufacturing Execution System?
Research by PwC suggests that companies who embrace MES will have an advantage over their competitors.
Their report talks about:
- 30% increases in productivity through increased machine uptime and usage.
- Reduced time to market for new products.
- Mass Customisation – Competitive advantage through meeting customer demand with ‘make to order’ products.
Companies who have implemented MES, have reported ROI from cost savings (better use of labour and machinery) by 3%. Also, additional revenue (new digital products and data analytics services) by 3%.
The 5 Key Components of a Manufacturing Execution System
When implementing any new system into your manufacturing process, there are quite a few elements to consider before you introduce something that doesn’t suit your company’s needs.
There’s no question that an MES adds value to any given manufacturing company. But this type of system offers an extensive list of functionalities. This is why you need to establish exactly what they can do and how they can benefit your specific company.
Before disrupting your operations by implementing a new system, it’s important to consider all the variables.
1. Planning your manufacturing process
The features for this within a MES should allow you to do production planning, production scheduling and assigning different work centres and people across a site or multiple sites.
There’s sometimes a little bit of an overlap between an advanced planning and a scheduling system. Typically, it should connect to your ERP system, pulling in all of the incoming works orders, sales orders or build-to-stock orders.
The mes should understand what the routing is for the product, or what the labour machine requirements are. It should allow you to slot those into your production calendar and let you know whether you’re going to achieve the expected delivery date or not. It should also let you know if there are any problems, or if you need to add in some extra resource or move your schedule around.
2. Live feedback
A MES should give you live feedback on your manufacturing process. You should immediately be able to see what the overall status is in terms of efficiency, or where specific manufacturing orders are.
This resolves the pain of walking around your factory looking for paper documents or trying to find an order for a specific customer. It also eliminates all that wasted time it takes to pull the efficiency data from your different work centres and compiling it into a report to see how well you did the week before. In this regard, the features of a mes give you the ability to track work in progress; establish a routing for different types of products, and capture data from each of those products as it goes through the routing.
Additionally, there are abilities within the mes to schedule or trigger maintenance tasks based on the manufacturing process. Often, this is an add on module or another integration, to complete any tasks required to maintain your process.
The minimum requirement of a mes should be the ability to put in calibration checks, station cleanliness checks and to schedule those in, as and when they are needed. For example, the mes can connect to a filter switch and when that switch closes or trips, it triggers a change of filter task to the maintenance department. It’s a nicely integrated system that responds to your manufacturing process as quickly as possible and as efficiently as possible.
3. Quality features
These relate to improving the quality system within your business, making it easier to maintain and implement, with less admin.
This includes things like having standard operating procedures and work instructions that operators can follow. Whether that be to follow an assembly or semi-manual process, or for work instructions, showing how to set up or change a machine before switching to monitoring the machine as it goes through a batch.
These features help to standardise processes across a business, making sure that when there’s an improvement in quality, everyone steps up to that level at the same time.
Quality Checks
Another feature for quality is the ability to have quality checks interspersed throughout your process. As a result, the issue of the huge amount of re-work at the end of the line is avoided.
A MES can intersperse checks as and when the process happens. For example, have you fitted the correct circuit board at the stage where that’s done? If not, and the issue is captured at that point and fixing the problem is easy. All it needs is to be swapped out and put it straight back in. If you don’t catch a problem until the end of the line, it means stripping everything back. The amount of rework and the cost of that to the business is ridiculous. A system that lets you put quality and process integrity checks early on, is an essential part of a MES in helping you maintain better quality.
Digital Product Records
Following on from that, another key area to focus on is having a fully traceable digital product record – sometimes called a manufacturing traveller or a job pack.
As your product goes through the manufacturing process, it should be completed and documented automatically. No more filling in paper documents with signatures, scribbling in pencil, crossing out and waiting for it to be fixed at a later date. Instead, you should have a simple digital, fully traceable record showing who did what, when they did it and what exactly they did. For example, pulling in batch numbers and serial numbers of components or batches of materials that have been used.
All of these features give you a solid quality system and set of tools that easily help you implement and maintain your quality system.
4. People Management
A MES should have tools to help track and manage the people within your manufacturing process.
Features that you’re looking for here, are skills matrix. The ability to manage who’s trained to do what process, on what type of product line. It makes it easy to manage who’s allowed to do what. For example, if someone is not trained, they will not be able to start the machine, and system will lock them out. This makes your compliance with the standards and audits much easier.
Time Tracking
There are standard times for each of your processes so, when everyone scans onto a work order, the mes should track how much time they’ve spent on each stage of the process.
It should record that information and give you reports, so you can see if your standard times are correct. As a result, you will know if you need to go back to your customer to do a requote for a job because you’ve budgeted for two hours and it actually takes four hours.
Time tracking down to that granular level can really help you spot and identify issues like opportunities for retraining; if a work environment isn’t set up correctly for particular processes; or if the tool positioning doesn’t make sense, making it difficult to do certain jobs.
5. Reporting
One of the big time-savers and headache relievers, particularly for managers and directors, is that a MES can automate your entire manufacturing reporting process.
The process of having people manually collecting data, putting it into Excel spreadsheets or creating charts, should all be eliminated. Every top level KPI you have and all the supporting data, should be captured by the MES to automatically generate a report.
If they’ve dropped below or outside the performance targets, it should ideally, send a weekly notification telling you that you’re below target performance and you need to do something about it. Reports like OEEs, first time through cycle times, or a statistical process control. At a minimum, your MES should be covering all these areas and be able to automatically generate that information for you, so you don’t have to.
Summary
To summarise, the 5 key components of a mes to give your business the biggest benefits are:
- Planning and scheduling features.
- Process related features – so that you can track work in process in your factory as it goes through the routing.
- Quality related features – work instructions and quality reports in-process checks.
- Features related to people – a minimum of skills matrix and time tracking.
- Automated reporting – to obtain custom reports for your exact KPIs and a few levels below, so you can drill out the details with your supplier.
Unleash the Power of Digital Manufacturing in 5 Steps
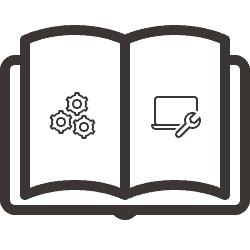
Are you ready for a Manufacturing Execution System?
Once a company is convinced of the benefits of implementing an MES within their company, the next stage is to assess the companies Digital Readiness Level (DRL). This will help you to understand what will be required to create a connected factory.
Our assessment of the key stages and requirements for implementing a Manufacturing Execution System are:
- Big data from machines, manual processes and PLCs needs to be acquired and networked across the factory.
- Big data needs to be analysed and converted into smart business data.
- Machines should then be able to make the business decisions currently being made by people.
“In the future, your IT infrastructure may be more valuable than your production assets”.
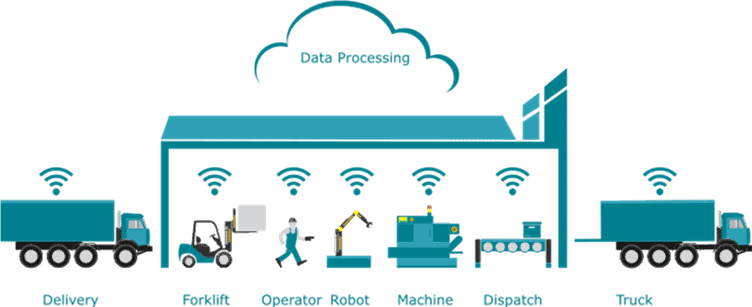
The major benefit will be the cost savings from better use of labour and machinery. There can also be additional revenue from new digital products and data analytics services.
Unleash the Power of Digital Manufacturing in 5 Steps
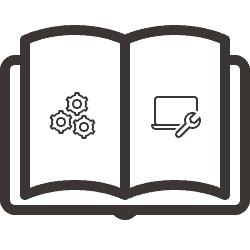
Step 1 – Creating a Secure Networked Factory
Benefits of a Manufacturing Execution System are achieved when computers can collate production data and make production decisions that are currently made manually. The first step in implementing this is connecting each production operation and machine with a secure network connection.
Secure Local Networks
The majority of installations we have been involved in have had secure local networks for production lines. They are connected to the internet or corporate network, through a gateway computer with TLS/SSL Encryption. The connections between production devices, gateways and the processing and analytics services in the cloud or on corporate networks, must have Confidentiality, Integrity and Availability (CIA).
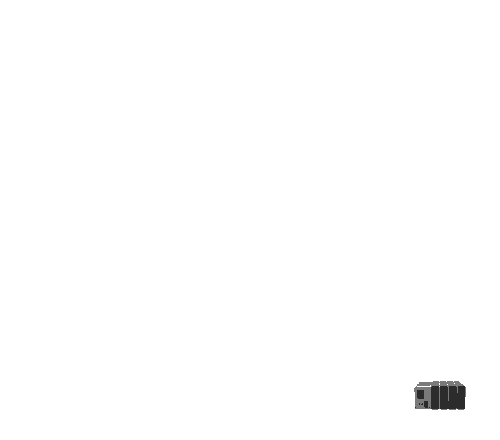
By following the key rules of the CIA, a system will have:
- Confidentiality – the ability to hide information from those who are not authorised to view it. Cryptographic encryption must be used to ensure confidentiality.
- Integrity – this ensures that the data received is an accurate representation of the data transmitted from the source. Devices should use cryptographic hashing to ensure data is not corrupted.
- Availability – ensures that the data is available to be accessed by the authorised viewer at any time. Devices must use cryptographic certificates to prove who they are.
Benefits of a CIA System
Firstly, the reliability of the production line is not reliant on the internet or corporate network connection. Secondly, it also has security benefits. Each machine network connection requires lower security standards, as they are not directly connected to the internet.
Custom machinery may be using industrial protocols like Modbus or OPC to connect to the Gateway. This ensures the Gateway to Cloud/Corporate Network is the main focus of secure local networks.
When configuring a network like this, the Gateway Hub computer will need 2 network ports. One for the local network using a fixed IP address and a second for connection to the internet or corporate network, using a TLS/SSL Encrypted connection.
The local network should then be connected with fixed IP addresses to all devices and machines in the production line.
Example
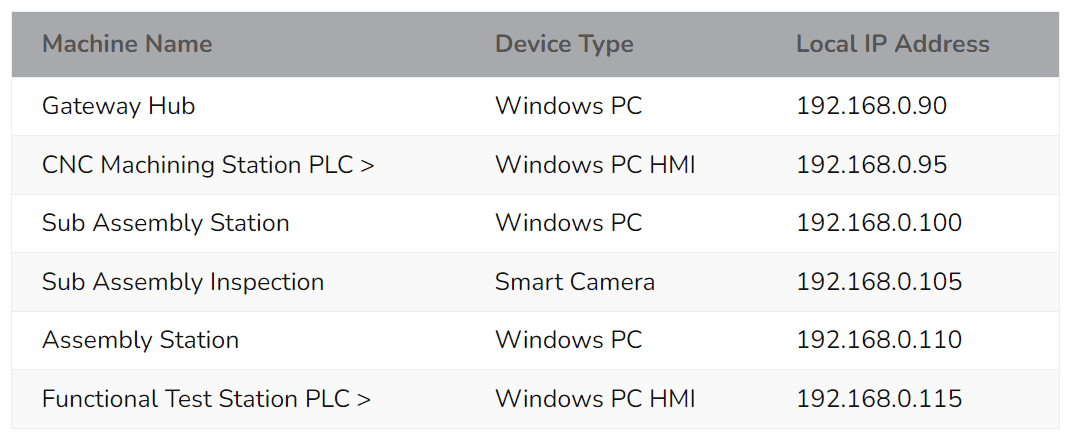
Using this network configuration, the Gateway PC will manage to communicate with the wider factory network. For example, to acquire production order data. The local network will be used to guide and manage the production process.
In addition, a local production database can be installed on the Gateway PC to store local production data. The Gateway PC polls each production device to check their status and ensure they’re capable of performing production operations.
Distributed Devices
Local networks are not an option when production equipment is located at remote locations. In this case, the only option is to directly connect machines and devices straight to the internet. This requires more stringent security procedures on the machine connection, to reduce the risk of attack onto production equipment.
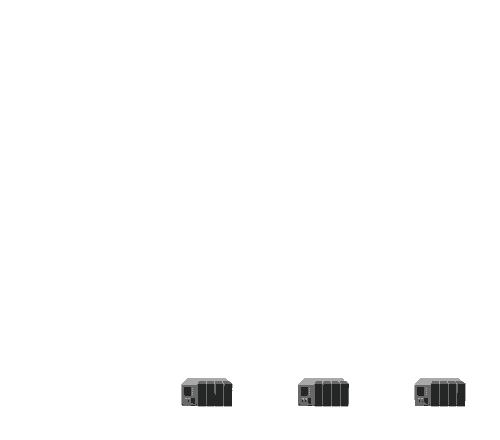
Under those circumstances, an encrypted connection from the device to the hub is required. This is because the distributed devices are susceptible to attack from outside the organisation.
Building a secure, reliable network is a key foundation of all Manufacturing Execution System solutions and should not be overlooked.
Step 2 – Communicating with Devices
Once a secure network is in place enabling a connection between production devices, a system must be created that will allow production machines to communicate with each other.
There are two main reasons for enabling production devices to communicate:
Monitor Machinery Status
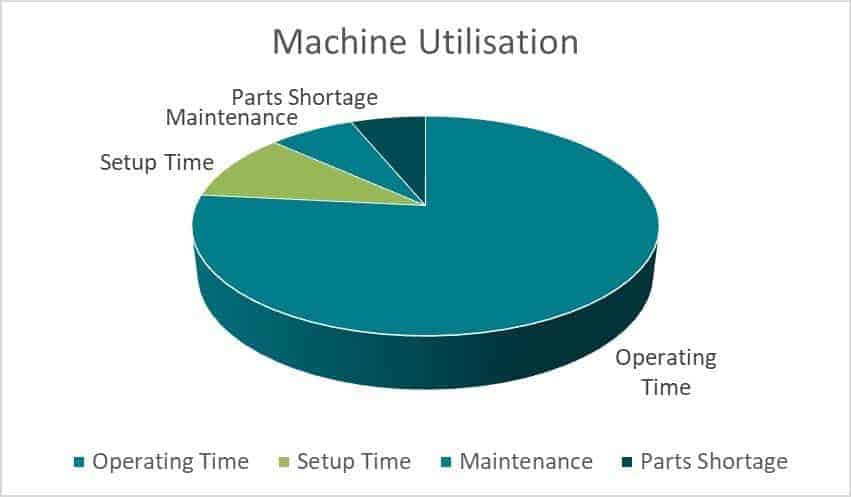
Acquiring and storing machinery status, health and production data enables you to perform machine data analysis to predict its performance. Doing this also helps you decide when and how the machine should be used. Ultimately, it improves its production efficiency and machine utilisation.
Control the Production Process
Sending commands to the production equipment to control what production processes to perform, reduces manual interaction and decision making within the production process. This makes the production process more efficient and more consistent.
Taking out the manual decision making of which program a machine should run, and having a software application make that decision, raises several keys benefits:
- The risk of making production mistakes are greatly reduced. This is because the correct machine program and setting can be configured correctly from the product’s routing and Bill of Materials (BOM), as opposed to selected manually from a work instruction.
- A greater variety of different products can be routed through the same production line, with extremely small batch sizes. As a software application selects the new machine configurations for each new product, change-over times can be drastically reduced between different parts.
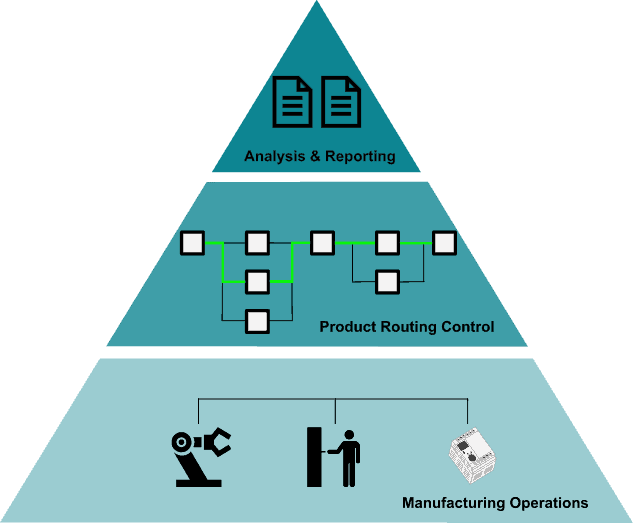
An Example of an MES where a Software Layer will perform Automated Product Routing
- The result of each production operation is recorded. Consequently, the production managers can instantly see the current production status of products moving along the production line. Product certifications can be automatically created and submitted directly to customers.
Connecting Devices
There are several types of manufacturing processes to connect to. Let’s simplify them down by categorising them into manual and automated processes. Manual processes are primarily controlled by a human operator. Automated processes are primarily controlled by an automation device, for example, a PLC or robot.
Each process must acquire data from the production process, then broadcast its data out using a standardised data format. This will be a data formatting schema that can be used for every manual process, machine or device. It contains the structure that allows software applications to understand the type of device sending the production data, as well as the production data characteristics contained.
Connecting Manual Process
Any manual or semi-automated process means we need to add sensors and a User Interface (UI). This gives the manual operator instruction of the manual process being performed and feedback on the process results. The process HMI and process sensors must then receive production information and send production data out, that the networked production line can understand and process.
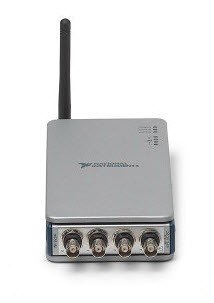
A Wireless Data Acquisition (DAQ Device)
To implement a system like this requires intelligent Industrial Internet of Things enabled sensors. Or alternatively, regular sensors connected through a device that can process incoming commands, then broadcast that sensor data out using a standardised data format.
Connecting Automated Machinery
If a process is automated a device will be controlling it, such as a PLC,Robot controller or Smart Tools. To connect these types of devices together an industrial protocol is used. The right type of protocol often depends on whether it can be supported by the PLC or robotic device that controls the process.
There are numerous established industrial protocols existing today, including:
Each of these industrial protocols can communicate with computers using an Ethernet network connection. A key requirement for the system is that there’s a software layer sitting between the devices that use the machine-specific protocol for each device. This software layer can then, in a generic format, broadcast the current machine status. It can also receive and send commands to the machine, using a protocol that it understands.
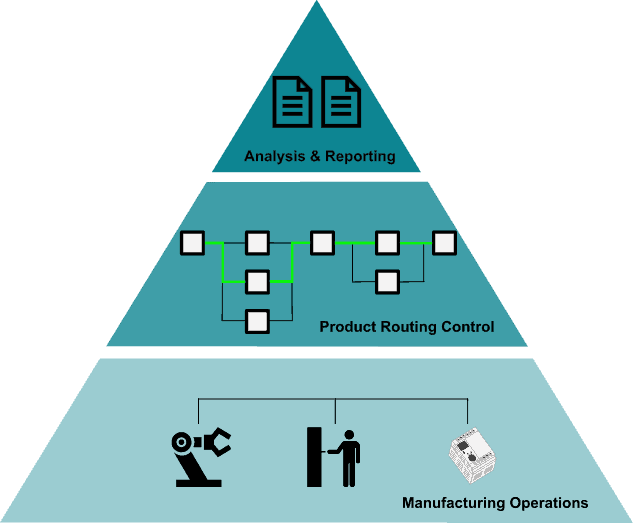
An Overview of an MES System, where manufacturing devices communicate through a Software Communications Layer.
As an example of this, we have developed our Manufacturing Execution System, Tascus, to have a device communication software layer that can communicate with any industrial protocol. It acts as a software layer to send and receive information to each manufacturing process. The Tascus software layer then stores its production data in a SQL Database for analysis and production tracking.
Step 3 – Connecting Manufacturing Processes
Connecting manufacturing processes is the first step in creating a paperless factory. This can deliver large increases in production efficiency and reduce the lead time of manufacturing products.
Many manufacturing systems control product routings manually. A bill of materials and job routing will be developed for a product. This will be printed out and carried along with a batch of product through a factory with various manufacturing operations. This requires planners, supervisors and production operators to review each product routing and decide what should happen to the product batch next.
By connecting manufacturing processes together a Manufacturing Execution System can perform all the product routing. It can consequently, communicate directly with production machinery to select the correct production process for each product batch.
Optimising Product Routing
When all production equipment is connected to the production system, the software application controlling the process has a large amount of data about the machinery and production equipment throughout the entire process. In addition, a software application can perform more analytics and quality checking on products as they progress through the factory. As a result, product routings can be changed based on feedback from production data, or on data from production machinery further down the production line.
The production software optimises the production process by adding logic to change routing:
- Bottlenecks can be avoided by balancing product routing against current process times.
- When sales order volume changes, the product can be rerouted automatically through the fastest path to delivery.
- New products can be routed quicker, with less manual decision making on the shop floor.
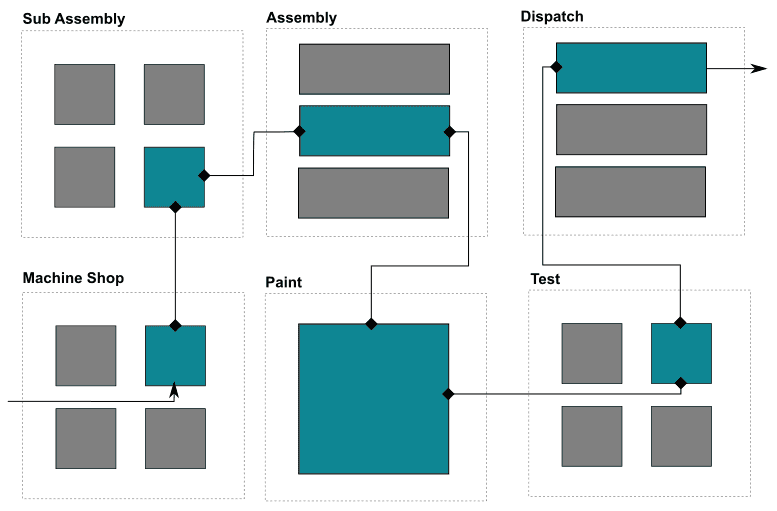
An example software HMI layout of a production facility with product routings highlighted.
Automatic Delivery of Job Packs
The software controlling the production systems knows all the production information about the part coming in to be manufactured. It can, therefore, be connected to CAD and ERP systems, to deliver the full job pack with manufacturing information to the production operator.
This ensures that the correct information is delivered for each product when it is required. It also makes the production of small batches of the product easier.
Guided Assembly
Human Machine Interfaces (HMIs) can be used to display production work instructions, guiding the operator through any manual production process. It displays production feedback from machinery that is needed for any decision making that the operator needs to take.
Automatic Delivery of Job Packs
The software controlling the production systems knows all the production information about the part coming in to be manufactured. It can, therefore, be connected to CAD and ERP systems, to deliver the full job pack with manufacturing information to the production operator.
This ensures that the correct information is delivered for each product when it is required. It also makes the production of small batches of the product easier.
Guided Assembly
Human Machine Interfaces (HMIs) can be used to display production work instructions, guiding the operator through any manual production process. It displays production feedback from machinery that is needed for any decision making that the operator needs to take.
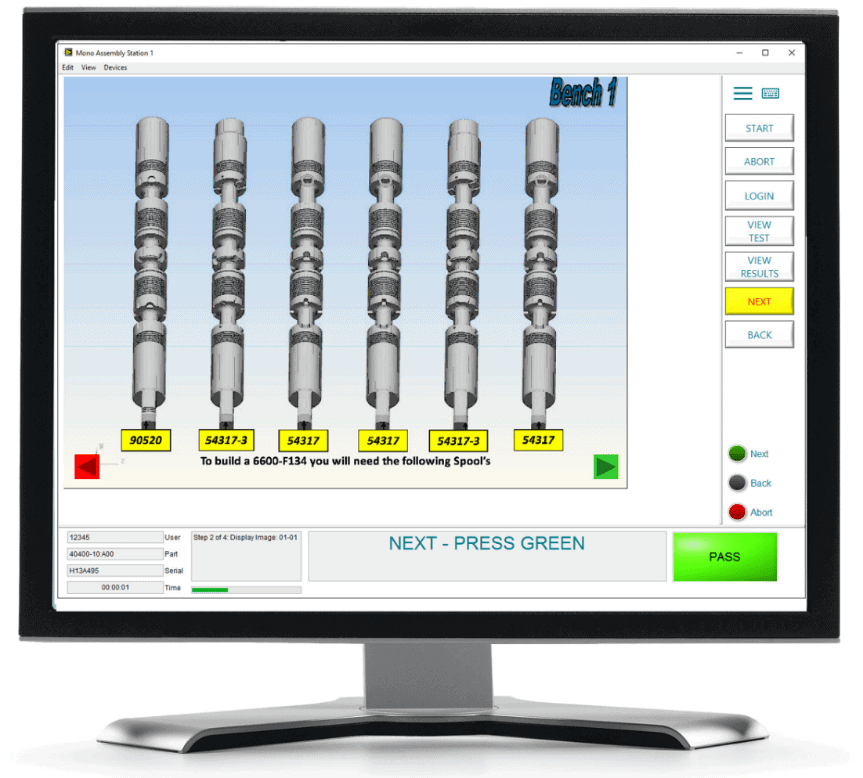
A Production Line HMI
When guided assembly stations are combined with sensors, barcode scanners and RFID tag readers, a trackable and traceable production line can be built. As the product moves along the production line, the software system records each manufacturing operation that has been completed. It can also record component details that have been used in the product.
All of the information can be stored in a production database. This allows product reports to be generated, detailing all manufacturing operations performed and all components used during manufacture.
Step 4 – Improving Your Business with Production Data Analytics
Once manufacturing operations are connected to IT systems, large amounts of production data can be gathered. However, it then needs to be converted from large volumes of unsorted production data, into data that is relevant to business processes. By performing automated analysis on the raw production data, the data can then be used to make business decisions about which manufacturing processes need further optimisation.
By using this data as an additional tool to help make the right business decisions, companies will have the advantage of continually improving their manufacturing operations. Businesses are using this information to:
- Increase manufacturing efficiency.
- Improve product quality.
- Expand their product
Production Planning
When the production system is storing data at each manufacturing operation, product routings and timing can be optimised.
The timing and product processing data that is stored can help identify underperforming machines, areas and operators.
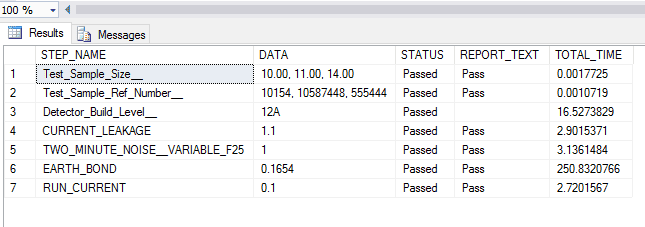
A Production Data Report with Operation Times
Maintenance
On each production machine, data can be acquired from its sensors. However, this needs to be processed in a way that’s relevant to machine expected life and service intervals.
Typical routine maintenance schedules will identify a fixed timescale for replacing machine components. However, this may be costly if the time schedule is either underestimated or overestimated.
During a recent project, we implemented a component life tracker that uses system pressure transducers. It calculates the expected life of system components, based on the time spent at different pressure levels. When the machine sits idle or performs low impact manufacturing process, the deterioration of system components is lower than when the machine performs near its maximum operating conditions.
By processing information taken from sensors and using it to predict machine component life, decisions about when to replace machine components can be optimised. This gets the maximum life from components and prevents unexpected machine failure.
New Digital Products
Imagine a company that creates highly complex control systems for automotive vehicles. Each complex component that is produced must then be assembled into a larger even more complex vehicle. The interface between the two is critical for the correct operation of the vehicle. So, when the customer drives it away, every aspect of the control of the vehicle feels right.
A client of Metis Automation does exactly this. As a result, they’ve been able to offer an additional product to each of their customers. A digital file copied over with every product shipped. This file contains the control configuration settings formatted in a way that the customer’s IT system can import the file directly to the vehicle that the component has been fitted to.
As the vehicle passes along the production line, it moves through an RFID scanning gate which detects all the information stored in components fitted to the vehicle. The IT system then looks up the configuration and production data for those components.
This replaces an extremely manual system where each vehicle would be manually tuned at the end of the production line, to obtain the optimum control configuration by trial and error.
Benefits of an Automated System
There are two main benefits to this new automated system. Firstly, it’s much more efficient as it removes lengthy manual tuning operations. Secondly, it’s much more effective and repeatable, as it takes out the subjectivity associated with manual tuning operations.
To our customers, the benefits are:
- Increased revenue from add on products.
- Differentiation from competitors who are not offering this service.
Implementing a Manufacturing Execution System in your business
In this guide, I’ve outlined the key areas to be implemented when creating a Connected Factory with an MES System. We have applied our experience from automating processes and creating connected factories.
Ignite Your Digital Transformation!
Let’s talk! Book a 1:1 call with our Chief Technical Officer to discover what your journey towards digital transformation could look like.