Investing in new production processes is a major step for any business. It requires balancing of the costs in time and money versus the benefits the business will reap in the future. Using an MES helps you succeed by focusing on what your customer wants at every point on the shop floor.
Here, I’ve summarised some of the key benefits our manufacturing clients have realised following their adoption of paperless manufacturing software.
Business Growth
By using an MES, the specific sequence of tasks required for reliable, repeatable production processes become defined for your business. As the business grows, this helps production processes to scale by ramping up, using the proven processes already in place.
A client created a production line driven by an MES to meet production requirements for a new customer. Once they had used the MES to define the production steps operators must complete, they were able to ramp up production volume by adding extra shifts with minimal training. As orders increased further, they created an additional two production cells driven by the same MES to meet demand.
Competitive Advantage Through Innovation
An MES allows the capture of a large volume of data from the shop floor. This can then be analysed to identify opportunities for product or process improvements.
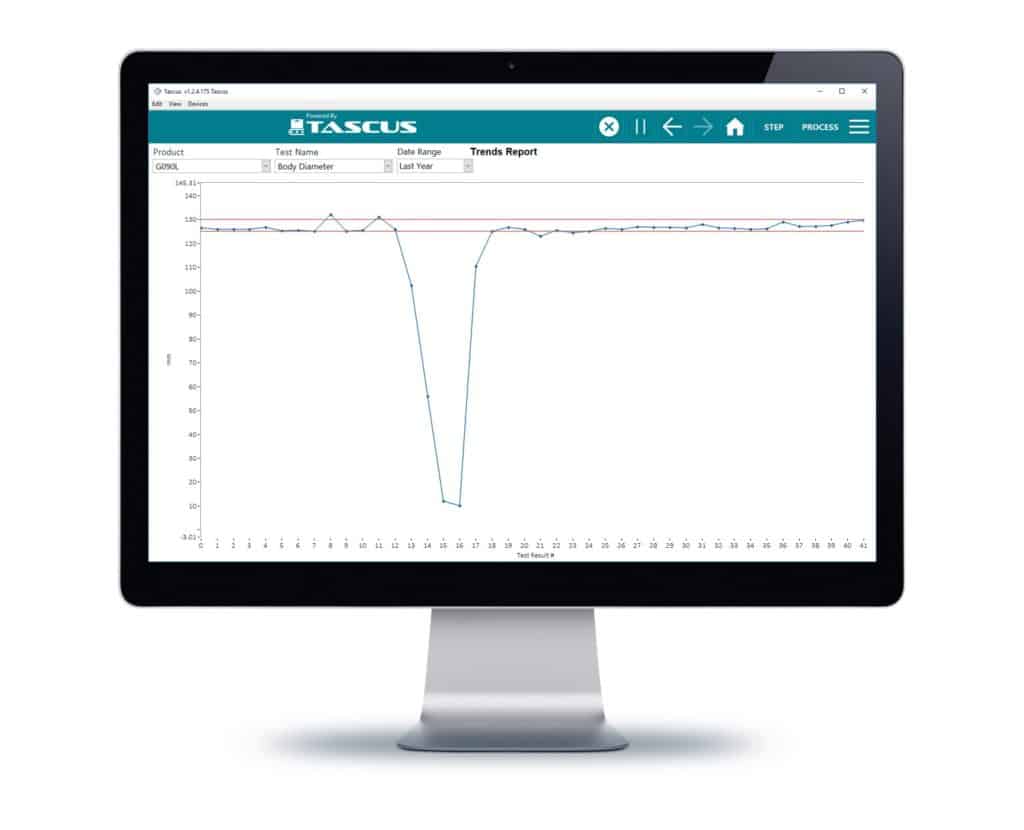
Trend reports of manufacturing data allow you to quickly identify opportunities for product and process improvement
The semiconductor industry is a classic example of using large volumes of data from production processes to better understand their processes. They use this data to make better semiconductor chips. It also enables them to put more transistors on a chip. The manufacturers that understand their manufacturing process best, are able to create the best performing, most innovative products.
Building Trust With Customers
Using an MES provides assurance to your customers that important production processes will be adhered to, and also that there will be a repeatable system for creating their products.
Clients in the automotive industry use our MES software Tascus to assist with their Production Part Approval Process (PPAP). This is a strict process during which manufacturers must produce data to prove they can meet the manufacturability and quality requirements of the parts supplied to the customer. Furthermore, they must also prove that the manufacturing process has the ability to produce the part consistently, during the actual production run. An MES helps by automatically capturing the required data and enforcing that the production process is maintained.
Enabling Global Expansion
Whether you are creating a new production facility down the road or across the globe, having standard production processes defined using an MES will enable you to transfer production reliably and repeatably. By tracking production performance using standardised reports from the MES, you can also perform like for like comparisons across sites.
Clients with multiple locations worldwide store their production data on a centralised server. This helps them to see global trends across product families, then quickly identify and address any issues affecting production.
Reducing Litigation
By having a traceable record of each product, you have the evidence to combat customer complaints when you were not at fault. If suppliers’ component problems arise, you can contain product recalls to only the affected items, therefore, minimising disruption and cost.
Our clients use the traceability features of our MES software Tascus to quickly identify which products have been shipped with specific batches of components. If a service issue arises where a component needs to be replaced, they can quickly run a report to identify the affected customers. This minimises disruption and cost of servicing.
Cost Savings
Some production processes have large amounts of paper documentation to record quality checks and serialised components used. The use of an MES can reduce data capture time and increase labour efficiency. An MES can also be used to capture production cycle times for each production step. By using this data and comparing to standard times, it can identify and solve problems causing delays in the process.
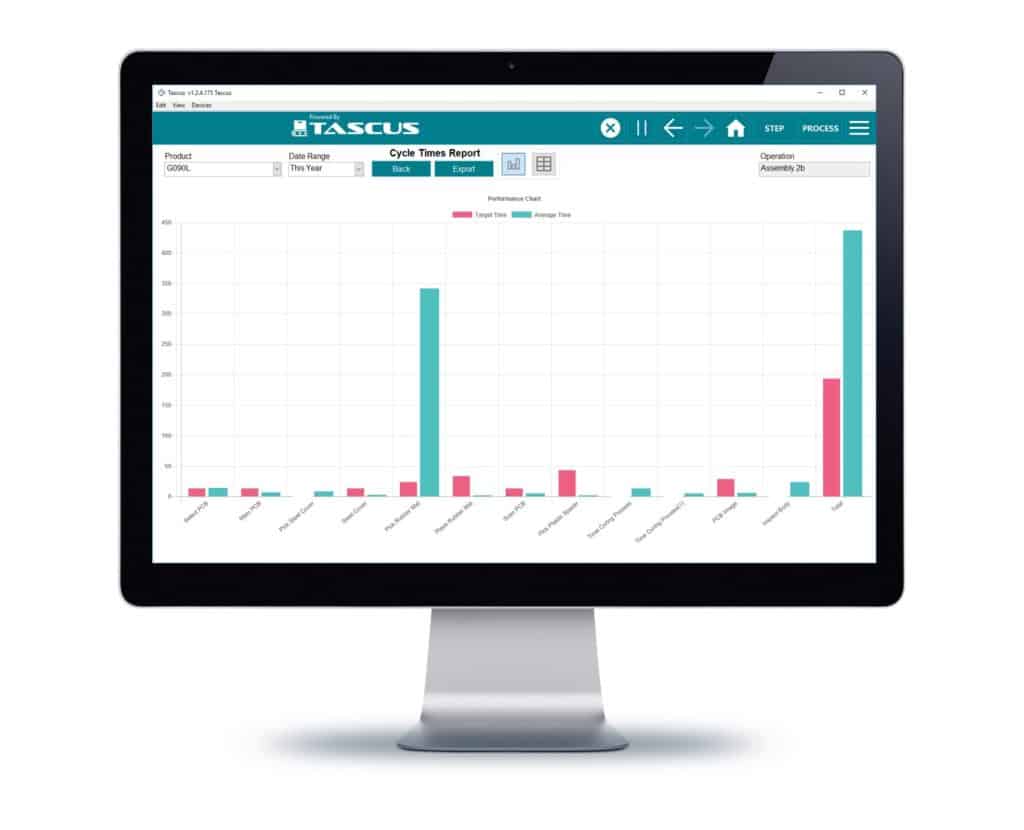
Production cycle times reports enable you to quickly identify production operations taking longer than expected
Several clients had lengthy paper-based manufacturing traveller documents. By replacing these with paperless manufacturing software, they achieved a 15% productivity increase leading to increased production output.
Enabling Culture Change
Using an MES can enforce quality and help the adoption of a right-first-time culture at every step in the process. When an MES is configured with quality checks throughout the production process, products that fail any checks cannot progress forward until the issues are fixed. Costs to resolve quality issues are much lower when they are detected early on in the manufacturing process rather than at the final quality inspection.
Clients have configured our MES software Tascus with quality-controlled stage gates in their production process. This ensures that only products that have successfully completed all operations can progress to later production processes. This ensures production operators are focused on following the production process and building products that will pass the next stage gate.
Unleash the Power of Digital Manufacturing
Download our free Digital Transformation Starter Kit to set the gold standard for operational clarity and excellence.