- Assets – putting a simple traffic light system to see how well they’re running.
- Products – get some updated visibility as to where they actually are in your process and tell you customer about it.
- People – understand who needs assistance, extra training, look at issues in their work area.
- Process – look for idle downtime, understand the reasons and cut it down to improve your lead time.
Unleash the Power of Digital Manufacturing in 5 Steps
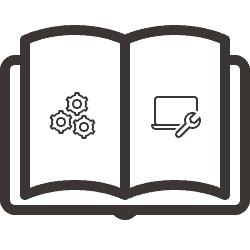
There is also a feature we’re developing which is going to be based on meeting the standard time for a process and all of the delivery schedules. Tascus will send out notifications to a supervisor when actual times are starting to lag behind standard times. They can jump in, understand what’s going on and resolve the problem straight away.
[/et_pb_text][/et_pb_column][/et_pb_row][/et_pb_section]Process
Optimise The Process
One thing that often gets overlooked when improving efficiencies in manufacturing plants is what happens in between manufacturing operations.
You might have a very efficient machine running at a high OEE, and have optimised your labour activity.
Often the next opportunity for efficiency improvements is to work out what is causing downtime in between operations. So as a manufacturing order moves through the factory, how long is spent idle waiting to start the next process in the manufacturing routing?
We’ve had some customers who’ve managed to cut their lead time in half just by analysing what issues were causing orders to sit idle between several manufacturing processes.
Track & Visualise The Entire Process
They did this by tracking the manufacturing order start and end time at each stage, then classifying the reasons for it being held up before starting the next process.
They put that data into a pareto chart using a spreadsheet and then focused on resolving issues that caused the most delays and disruptions first. Often it’s 20% of issues that are causing 80% of delays.
At the end of that exercise, they cut their lead time in half, from eight weeks to four weeks.
In terms of customer service, that’s a massive competitive advantage if you can deliver in half the time that your competitor can.
Summary
To summarise, there are four areas that you can increase the visibility of the production process:
- Assets – putting a simple traffic light system to see how well they’re running.
- Products – get some updated visibility as to where they actually are in your process and tell you customer about it.
- People – understand who needs assistance, extra training, look at issues in their work area.
- Process – look for idle downtime, understand the reasons and cut it down to improve your lead time.
Unleash the Power of Digital Manufacturing in 5 Steps
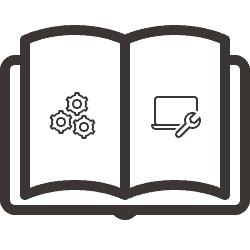
A more advanced way would be to connect directly to the machine, or attach sensors to it. As a result, your manufacturing manager in the office or overseas can see the information straight away. He will then understand what he needs to focus on, as opposed to having to ring someone up or having to walk around, before focusing on what needs to be done.
[/et_pb_text][/et_pb_column][/et_pb_row][/et_pb_section]Products
World Class Order Visibility
Another way to make a big impact is improving the visibility of your products as they go through your factory.
A lot of companies take a customer order, process it, but it goes into the factory and then it just enters a big black hole. It reappears at some point in the future, ready for dispatch, with no updates in between. This leads to frustration and lots of manual chasing.
When you place an order with Amazon, you get update emails as your order is getting processed, picked, dispatched and due for delivery. If you can move towards offering that level of service to your customers, it’s going to give you a huge competitive advantage.
Track Your Products
A simple solution is to track of the works orders as they move through your factory. Identify the key processes in that a product goes through during it transformation into finished goods.
Tracking products can be done easily with:
- A spreadsheet
- An ERP / MRP system
- An online dashboard (like Trello – see above)
- Shopfloor data capture software
Having a solution like this could then be integrated with customer alerts. For example, emailing customers to tell them which stage their product is at and is X days from dispatch, would bring a brilliant level of service and would really set you apart from your competitors.
People
Establish Standard Processes
In all manufacturing businesses, there are production operators with vastly different levels of expertise working in processes that you expect to produce products of a standard quality, consistency, and at a good level of productivity.
Establishing standard working processes using visual work instructions, product routings, and standard operating procedures will help you to train new hires, and to establish best practices across the business.
Calculating standard times for each process is critical to ensure you can accurately cost jobs, and track production efficiency.
Track Efficiencies
Once you have established standard processes and times, you need visibility into how effectively each production operator performs.
Low efficiencies may flag up that they need additional training. It may also signify issues with the manufacturing process itself – often tooling or fixturing may need to be redesigned. Without tracking, some people may be struggling but they aren’t vocal, and don’t flag issues until you specifically ask them.
Tracking can be done with Time & Motion studies, although they can be time-consuming. or with shop floor data capture systems which can track, flag and alert actual times vs standard times. Some systems even flag using an Andon light, or send out email notifications.
We’ve been developing features in Tascus that can help, including sending out notification messages to the managers or supervisors. For example, if there’s some kind of delay in the line stop, they can send that request out straight away and get assistance rather than having to go around searching the shop floor for their supervisor.
There is also a feature we’re developing which is going to be based on meeting the standard time for a process and all of the delivery schedules. Tascus will send out notifications to a supervisor when actual times are starting to lag behind standard times. They can jump in, understand what’s going on and resolve the problem straight away.
Process
Optimise The Process
One thing that often gets overlooked when improving efficiencies in manufacturing plants is what happens in between manufacturing operations.
You might have a very efficient machine running at a high OEE, and have optimised your labour activity.
Often the next opportunity for efficiency improvements is to work out what is causing downtime in between operations. So as a manufacturing order moves through the factory, how long is spent idle waiting to start the next process in the manufacturing routing?
We’ve had some customers who’ve managed to cut their lead time in half just by analysing what issues were causing orders to sit idle between several manufacturing processes.
Track & Visualise The Entire Process
They did this by tracking the manufacturing order start and end time at each stage, then classifying the reasons for it being held up before starting the next process.
They put that data into a pareto chart using a spreadsheet and then focused on resolving issues that caused the most delays and disruptions first. Often it’s 20% of issues that are causing 80% of delays.
At the end of that exercise, they cut their lead time in half, from eight weeks to four weeks.
In terms of customer service, that’s a massive competitive advantage if you can deliver in half the time that your competitor can.
Summary
To summarise, there are four areas that you can increase the visibility of the production process:
- Assets – putting a simple traffic light system to see how well they’re running.
- Products – get some updated visibility as to where they actually are in your process and tell you customer about it.
- People – understand who needs assistance, extra training, look at issues in their work area.
- Process – look for idle downtime, understand the reasons and cut it down to improve your lead time.
Unleash the Power of Digital Manufacturing in 5 Steps
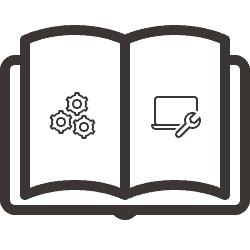
So, how do you get yourself into the know?
[/et_pb_text][/et_pb_column][/et_pb_row][/et_pb_section]
Check out our video below on the ways you can improve the visibility of your assets, products, people, and processes.
Here’s the 4 areas to improve visibility that I outlined in the video:
Assets
Identify Your Bottleneck Assets
So, the first area where there’s a quick win for improving production visibility is your assets. You may have some large assets or machines in your factory that you’ve invested a lot in. If you have some way of tracking the status and the availability of those machines quickly and clearly, it will help you plan better to keep those assets available and at full productivity.
For example, if one of those machines is out of service for a period of time, it can help you to plan which way to route that product quickly. It can also help you to focus on where to put resources.
If you’ve got key assets that are performing slower or have stopped, you will know what to focus on.
Traffic Light System
A simple way to do track asset status is a traffic light system:
Green – Running a Full Capacity
Amber – Running at Reduced Capacity
Red – Stopped / Unexpected Downtime
The easiest way to update status is to have the operator fil in a spreadsheet. Set the colour of an ‘Andon’ traffic light next to the machine, so it’s visible on the shop floor.
A more advanced way would be to connect directly to the machine, or attach sensors to it. As a result, your manufacturing manager in the office or overseas can see the information straight away. He will then understand what he needs to focus on, as opposed to having to ring someone up or having to walk around, before focusing on what needs to be done.
Products
World Class Order Visibility
Another way to make a big impact is improving the visibility of your products as they go through your factory.
A lot of companies take a customer order, process it, but it goes into the factory and then it just enters a big black hole. It reappears at some point in the future, ready for dispatch, with no updates in between. This leads to frustration and lots of manual chasing.
When you place an order with Amazon, you get update emails as your order is getting processed, picked, dispatched and due for delivery. If you can move towards offering that level of service to your customers, it’s going to give you a huge competitive advantage.
Track Your Products
A simple solution is to track of the works orders as they move through your factory. Identify the key processes in that a product goes through during it transformation into finished goods.
Tracking products can be done easily with:
- A spreadsheet
- An ERP / MRP system
- An online dashboard (like Trello – see above)
- Shopfloor data capture software
Having a solution like this could then be integrated with customer alerts. For example, emailing customers to tell them which stage their product is at and is X days from dispatch, would bring a brilliant level of service and would really set you apart from your competitors.
People
Establish Standard Processes
In all manufacturing businesses, there are production operators with vastly different levels of expertise working in processes that you expect to produce products of a standard quality, consistency, and at a good level of productivity.
Establishing standard working processes using visual work instructions, product routings, and standard operating procedures will help you to train new hires, and to establish best practices across the business.
Calculating standard times for each process is critical to ensure you can accurately cost jobs, and track production efficiency.
Track Efficiencies
Once you have established standard processes and times, you need visibility into how effectively each production operator performs.
Low efficiencies may flag up that they need additional training. It may also signify issues with the manufacturing process itself – often tooling or fixturing may need to be redesigned. Without tracking, some people may be struggling but they aren’t vocal, and don’t flag issues until you specifically ask them.
Tracking can be done with Time & Motion studies, although they can be time-consuming. or with shop floor data capture systems which can track, flag and alert actual times vs standard times. Some systems even flag using an Andon light, or send out email notifications.
We’ve been developing features in Tascus that can help, including sending out notification messages to the managers or supervisors. For example, if there’s some kind of delay in the line stop, they can send that request out straight away and get assistance rather than having to go around searching the shop floor for their supervisor.
There is also a feature we’re developing which is going to be based on meeting the standard time for a process and all of the delivery schedules. Tascus will send out notifications to a supervisor when actual times are starting to lag behind standard times. They can jump in, understand what’s going on and resolve the problem straight away.
Process
Optimise The Process
One thing that often gets overlooked when improving efficiencies in manufacturing plants is what happens in between manufacturing operations.
You might have a very efficient machine running at a high OEE, and have optimised your labour activity.
Often the next opportunity for efficiency improvements is to work out what is causing downtime in between operations. So as a manufacturing order moves through the factory, how long is spent idle waiting to start the next process in the manufacturing routing?
We’ve had some customers who’ve managed to cut their lead time in half just by analysing what issues were causing orders to sit idle between several manufacturing processes.
Track & Visualise The Entire Process
They did this by tracking the manufacturing order start and end time at each stage, then classifying the reasons for it being held up before starting the next process.
They put that data into a pareto chart using a spreadsheet and then focused on resolving issues that caused the most delays and disruptions first. Often it’s 20% of issues that are causing 80% of delays.
At the end of that exercise, they cut their lead time in half, from eight weeks to four weeks.
In terms of customer service, that’s a massive competitive advantage if you can deliver in half the time that your competitor can.
Summary
To summarise, there are four areas that you can increase the visibility of the production process:
- Assets – putting a simple traffic light system to see how well they’re running.
- Products – get some updated visibility as to where they actually are in your process and tell you customer about it.
- People – understand who needs assistance, extra training, look at issues in their work area.
- Process – look for idle downtime, understand the reasons and cut it down to improve your lead time.
Unleash the Power of Digital Manufacturing in 5 Steps
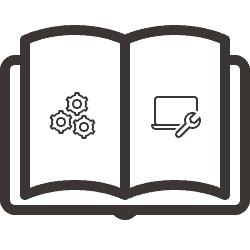
Improving Production Visibility for Successful Processes
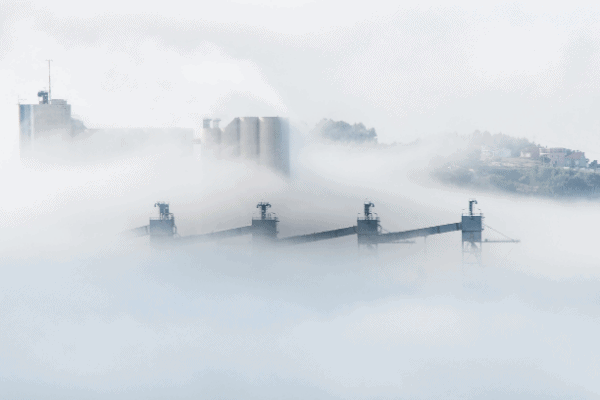
What does it mean to have good visibility of your production processes?
Well, simply put, you need to know exactly what’s going on in your production process in order to make the right decisions when it comes down to the crunch. When companies don’t have sufficient visibility, collecting data will become a timely and tedious operation.
What’s more, the data they’re collecting is probably out of date. This means they either can’t make the right decisions, or they’re unknowingly making wrong decisions that could cost them money.
To save your time, money, and valuable assets, you can start by taking small steps towards improving the visibility of your production process. Once you’ve achieved this, you can start focusing on the right areas that need the most improvement, growth, and time.
To be successful, you need to be in control and in the loop of your production process.
So, how do you get yourself into the know?
Check out our video below on the ways you can improve the visibility of your assets, products, people, and processes.
Here’s the 4 areas to improve visibility that I outlined in the video:
Assets
Identify Your Bottleneck Assets
So, the first area where there’s a quick win for improving production visibility is your assets. You may have some large assets or machines in your factory that you’ve invested a lot in. If you have some way of tracking the status and the availability of those machines quickly and clearly, it will help you plan better to keep those assets available and at full productivity.
For example, if one of those machines is out of service for a period of time, it can help you to plan which way to route that product quickly. It can also help you to focus on where to put resources.
If you’ve got key assets that are performing slower or have stopped, you will know what to focus on.
Traffic Light System
A simple way to do track asset status is a traffic light system:
Green – Running a Full Capacity
Amber – Running at Reduced Capacity
Red – Stopped / Unexpected Downtime
The easiest way to update status is to have the operator fil in a spreadsheet. Set the colour of an ‘Andon’ traffic light next to the machine, so it’s visible on the shop floor.
A more advanced way would be to connect directly to the machine, or attach sensors to it. As a result, your manufacturing manager in the office or overseas can see the information straight away. He will then understand what he needs to focus on, as opposed to having to ring someone up or having to walk around, before focusing on what needs to be done.
Products
World Class Order Visibility
Another way to make a big impact is improving the visibility of your products as they go through your factory.
A lot of companies take a customer order, process it, but it goes into the factory and then it just enters a big black hole. It reappears at some point in the future, ready for dispatch, with no updates in between. This leads to frustration and lots of manual chasing.
When you place an order with Amazon, you get update emails as your order is getting processed, picked, dispatched and due for delivery. If you can move towards offering that level of service to your customers, it’s going to give you a huge competitive advantage.
Track Your Products
A simple solution is to track of the works orders as they move through your factory. Identify the key processes in that a product goes through during it transformation into finished goods.
Tracking products can be done easily with:
- A spreadsheet
- An ERP / MRP system
- An online dashboard (like Trello – see above)
- Shopfloor data capture software
Having a solution like this could then be integrated with customer alerts. For example, emailing customers to tell them which stage their product is at and is X days from dispatch, would bring a brilliant level of service and would really set you apart from your competitors.
People
Establish Standard Processes
In all manufacturing businesses, there are production operators with vastly different levels of expertise working in processes that you expect to produce products of a standard quality, consistency, and at a good level of productivity.
Establishing standard working processes using visual work instructions, product routings, and standard operating procedures will help you to train new hires, and to establish best practices across the business.
Calculating standard times for each process is critical to ensure you can accurately cost jobs, and track production efficiency.
Track Efficiencies
Once you have established standard processes and times, you need visibility into how effectively each production operator performs.
Low efficiencies may flag up that they need additional training. It may also signify issues with the manufacturing process itself – often tooling or fixturing may need to be redesigned. Without tracking, some people may be struggling but they aren’t vocal, and don’t flag issues until you specifically ask them.
Tracking can be done with Time & Motion studies, although they can be time-consuming. or with shop floor data capture systems which can track, flag and alert actual times vs standard times. Some systems even flag using an Andon light, or send out email notifications.
We’ve been developing features in Tascus that can help, including sending out notification messages to the managers or supervisors. For example, if there’s some kind of delay in the line stop, they can send that request out straight away and get assistance rather than having to go around searching the shop floor for their supervisor.
There is also a feature we’re developing which is going to be based on meeting the standard time for a process and all of the delivery schedules. Tascus will send out notifications to a supervisor when actual times are starting to lag behind standard times. They can jump in, understand what’s going on and resolve the problem straight away.
Process
Optimise The Process
One thing that often gets overlooked when improving efficiencies in manufacturing plants is what happens in between manufacturing operations.
You might have a very efficient machine running at a high OEE, and have optimised your labour activity.
Often the next opportunity for efficiency improvements is to work out what is causing downtime in between operations. So as a manufacturing order moves through the factory, how long is spent idle waiting to start the next process in the manufacturing routing?
We’ve had some customers who’ve managed to cut their lead time in half just by analysing what issues were causing orders to sit idle between several manufacturing processes.
Track & Visualise The Entire Process
They did this by tracking the manufacturing order start and end time at each stage, then classifying the reasons for it being held up before starting the next process.
They put that data into a pareto chart using a spreadsheet and then focused on resolving issues that caused the most delays and disruptions first. Often it’s 20% of issues that are causing 80% of delays.
At the end of that exercise, they cut their lead time in half, from eight weeks to four weeks.
In terms of customer service, that’s a massive competitive advantage if you can deliver in half the time that your competitor can.
Summary
To summarise, there are four areas that you can increase the visibility of the production process:
- Assets – putting a simple traffic light system to see how well they’re running.
- Products – get some updated visibility as to where they actually are in your process and tell you customer about it.
- People – understand who needs assistance, extra training, look at issues in their work area.
- Process – look for idle downtime, understand the reasons and cut it down to improve your lead time.
Unleash the Power of Digital Manufacturing in 5 Steps
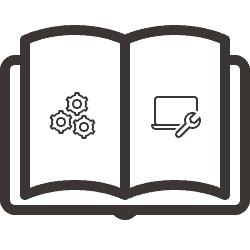