Preventable mistakes in the manufacturing process are frustrating and annoying for your customer. But, they are also low hanging fruit for business improvement.
When you have identified several mistakes that keep occurring in your manufacturing process or you have product returns from a customer, the next step is to resolve the issues and prevent the mistakes that caused those returns. By approaching this in a systemised way, you can create a big impact quite quickly.
Build a Team
Set up a team to address the mistakes in your manufacturing process, including:
- A Customer Representative
- Product Design
- Manufacturing Operations
- Quality
This ensures whatever solution you come up with, the customer will get what they want without affecting the product performance. By involving manufacturing and quality, you can come up with a solution that will work on the factory floor. You can also get buy-in from the entire operations team.
Identify Risks
The best place to start is understanding the knock-on effect mistakes made in manufacturing will have on your product. The fit, form and function of it when it gets used, or the safety of the product to the people around it. When you understand the risks, you can establish what level of things you have to do to reduce those risks to an acceptable level.
You can use a tool like a failure mode and effects analysis (FMEA). Sit down in a room and bounce around ideas. Come up with things that could go wrong, using past experiences or discussions with your customers. Identify what could happen and also, try to classify it into those categories of:
- Safety-Critical
- Fit, form and function
- Visual defect
By understanding the risk, you’re better placed in the later stages of a redesign, to know what you need to do to reduce those risks to an acceptable level.
Root Cause
When mistakes happen, sometimes it’s natural to quickly jump to the obvious answer of why it happened. However, I think it’s always worth using a technique like the 5 Why’s, to drill down to the root cause of the issue and to find the underlying reasons for why it happened. This, as a result, makes it more likely that the issue will never recur. Also, you will probably discover that the root cause is creating other mistakes as well. Here’s a quick example. So, if an operator fitted the wrong component into a product we first ask, ‘Why did that happen?’ A – Components look quite similar and they’re in the same place on a production line. ‘Why are they similar and in the same place?’ A – They come from the same supplier and are placed in the same location by the line supplier when he brings them out to restock the line. ‘Why do they do that?’ A – Because that’s the quickest way to do it on his route. In this example scenario, if we’d focused a solution on the operator who picked the incorrect component, then we haven’t resolved the entire problem. By drilling down a few levels, we’ve started to understand what we need to do to address the problem in its entirety. We need to come up with a solution that also addresses the placement, the picking and the storage of components on the line. As a result, this will prevent the mistake from happening again.Redesign the Process
1. Poka Yoke
The most effective way to prevent mistakes would be to “Poka Yoke“ (mistake-proof) the product or the manufacturing process. If you can mistake-proof, it means you’re eliminating the possibility that that mistake can ever happen again.
For example, to Poka Yoke a product, you could change a thread so it’s impossible to screw in the wrong component. To Poka Yoke the manufacturing process you could redesign the tooling or the fixture, therefore making it extremely difficult to fit the wrong components in the wrong place.
2. Alert
If Poka Yoke isn’t possible, the next option for redesign is to Alert & Verify. Using the previous example where there are two similar components that must be interchangeable, do something highly visual to alert the operator.
For example, put one component in a green bin and one in a red bin. At the point when the operator selects the component, make sure they have a visual alert that a component from the red bin must be used.
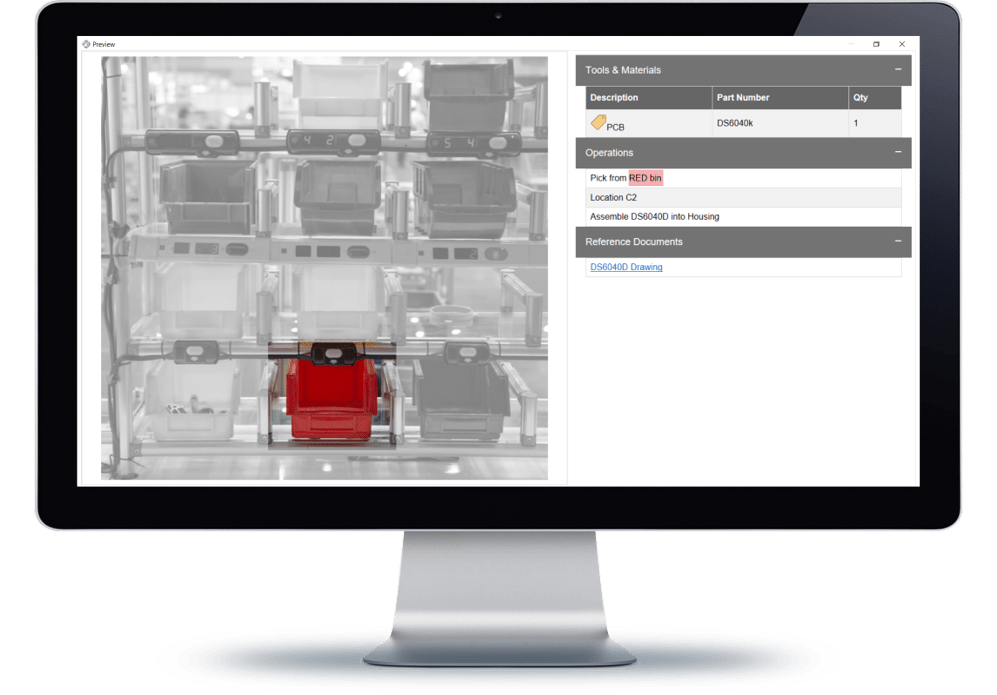
Alerting an Operator to Select the Correct Component Using Tascus
Another solution is to use a Pick to Light system, which automatically lights up the correct component to select. It can also be used to verify the correct component was selected.
3. Verification
There should be a verification immediately after the manufacturing process. Use functional test, visual inspection, or smart camera, to make sure a mistake has not occurred.
Don’t leave this verification until the end of the manufacturing process. The amount of re-work to strip a product right back, replace the components and repeat the manufacturing process is extremely costly and disruptive. So, putting a small, quick verification in immediately after the process is a much more effective way of ensuring no mistakes have occurred.
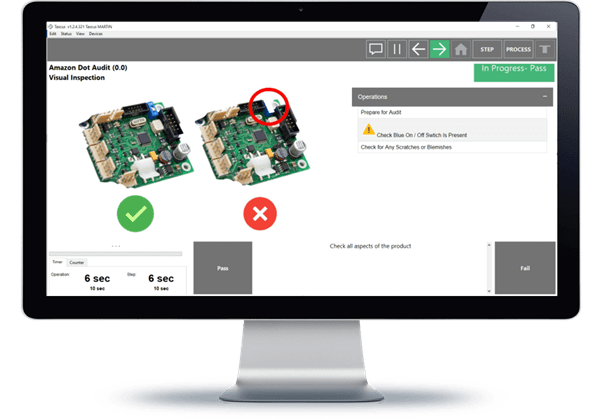
Performing a Visual Inspection using Tascus
Track Performance
Once you have implemented your redesigned process to prevent and detect mistakes, you want to know how effective it’s been. Identify a metric that’s an indicator of good product quality and requires low number of mistakes in the manufacturing process. Examples are:
- Number of Product Returns (should start decreasing)
- First Through Test (FTT) (should increase)
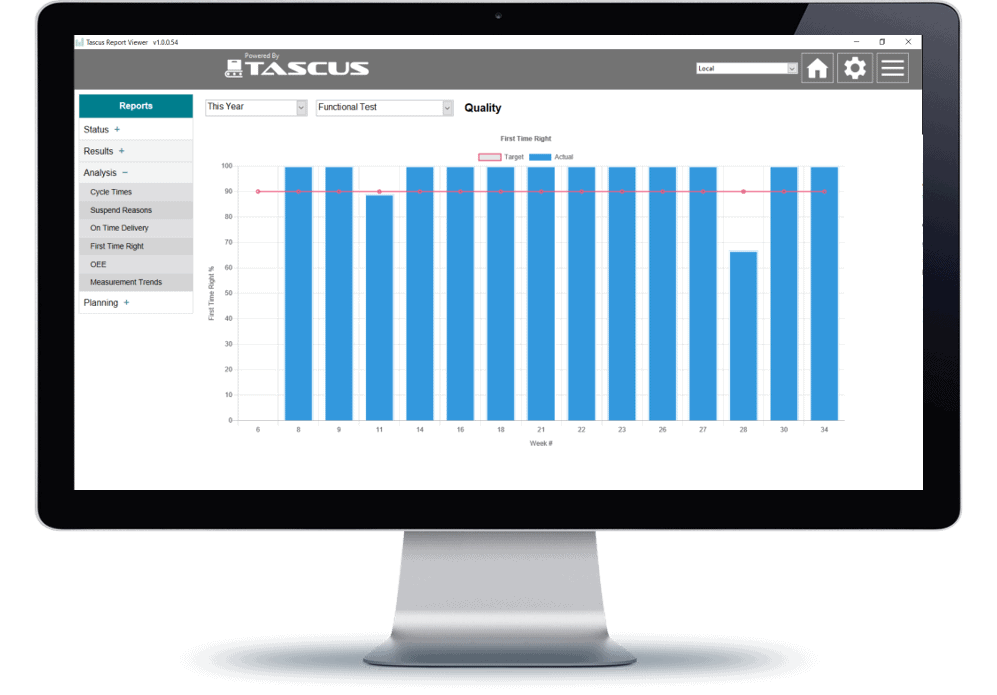
Automatically Track KPI’s Including FTT in Tascus
Start tracking daily/ weekly/monthly, to make sure the metric is going in the right direction. When you see the metric improving, the time and money you’ve spent redesigning the process is justified because it’s been effective. It may have saved your test time, rework and reduced costs of product returns. If you find the metric is not improving, it’s time to try another process re-design to try an alternative solution.
Summary
To summarise, there are 5 key steps for how to prevent and detect mistakes in the manufacturing process:
- Build a Team to address the issue
- Identify the Risks of the mistake
- Find the Root Cause
- Redesign the Process based on the root cause
- Track the Performance of the solution after you’ve redesigned your process
Unleash the Power of Digital Manufacturing
Download our free Digital Transformation Starter Kit to set the gold standard for operational clarity and excellence.