How does Connected Manufacturing affect production test systems in factories ensuring that high-quality products are shipped to customers?
Explore how Connected Manufacturing is being implemented in businesses, and how test systems need to adapt to be ready to capitalise on the opportunities of Industry 4.0.
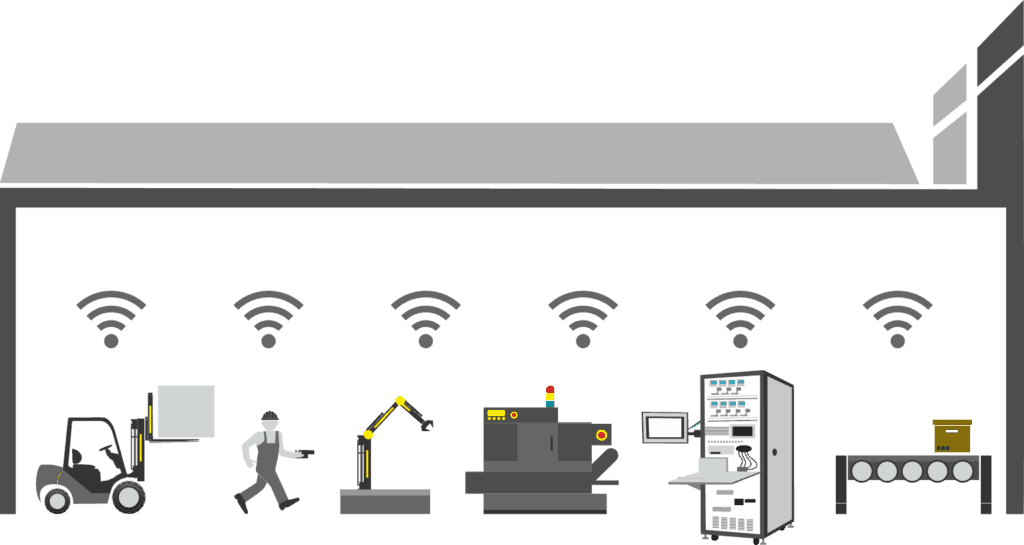
Several terms describe the introduction of connected manufacturing processes. Its a connected network that shares data, consequently allowing manufacturers to make better business decisions. Some of these terms are Industry 4.0, 4IR, Smart Factories and Connected Manufacturing.
In recent years there has been a revolutionary change, where manual and automated process are being connected to communicate with each other. Previously, standalone automated processes required some manual decision making – to define which processes to run and when maintenance should occur. This was generally managed using paper-based job cards and works orders. The introduction of connected manufacturing processes is consequently allowing these decisions to be automated.
An Automated Test System in a Connected Factory
Automated Test Systems have been around for over 20 years. They are an essential part of the quality control process in manufacturing organisations. Consequently, they are key to the production process and should be connected to other manufacturing equipment, so that test data can be shared throughout the factory.
The main feature of a test system in a connected factory is to communicate with other devices and share it’s test data throughout the factory. To perform this communication, an additional software module is required in the automated test software.
We call this a Production Data Interface. Its main job is to get data from other manufacturing processes, that can automatically control the test sequence. It must also store test data into the production data interface, that will be useful for subsequent stages of the manufacturing process.
By implementing this connected system, many decisions that are currently manual and time-consuming can be automated. This makes the production process more efficient and effective. As a result, production output, productivity and product quality is improved.
We create a software module that can communicate with the production data using a variety of different methods. The most common being a SQL database or a web server.
What are the Benefits?
Once connected test systems have been implemented, a number of business benefits can be achieved including:
- Increased production output by reducing production test bottlenecks in factories.
- Winning new business with higher-value customers who want production test data transmitted digitally, as soon as products are completed.
Some of these automated systems are distilled process, paint shops, and conveyors belts manufacturing.